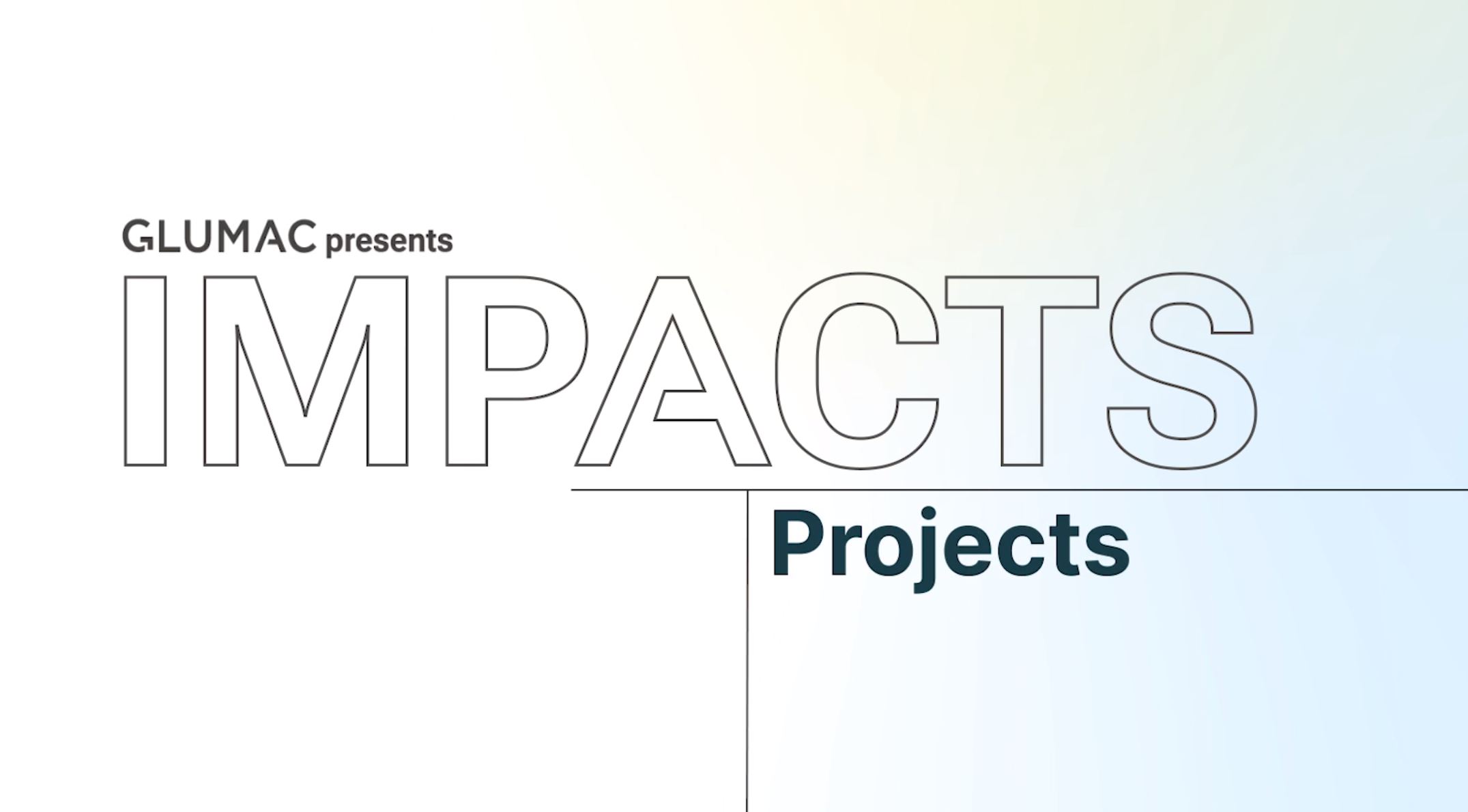
The battle for students’ attention in K-12 spaces is an enduring struggle. If you’re feeling like phones, social media, and a constant stream of content are making student attention spans shorter, you’re likely on to something.
Bad lighting isn’t helping either.
Thoughtful lighting design, with a particular focus on natural light, has demonstrated significant positive impacts on learning outcomes. And access to daylight has been shown to increase mood and attention levels. We’ve written before about the concept of circadian lighting and its impact on occupant well-being and performance. And some of its most apparent impacts come in the K-12 space, where studies have shown that exposure to daylight allowed students to finish math tests 20 percent faster and finish reading tests 26 percent faster.
But there’s more to getting good lighting than simply poking holes in the façade.
It’s safe to say that architects, school administrators, and lighting designers want windows and skylights in classrooms and adjacent learning spaces for their obvious benefits. However, this is rarely achieved through simply poking holes in the façade for large windows. How often have you sat in a hot conference room in the late afternoon as the sun beats down through the windows? To get this right, there are many geographical, meteorological, and spatial considerations to explore related to this during design, including:
- Distraction Free Daylight: It may be more effective to utilize clerestory windows or skylights in a classroom adjacent to a busy playground to avoid distraction.
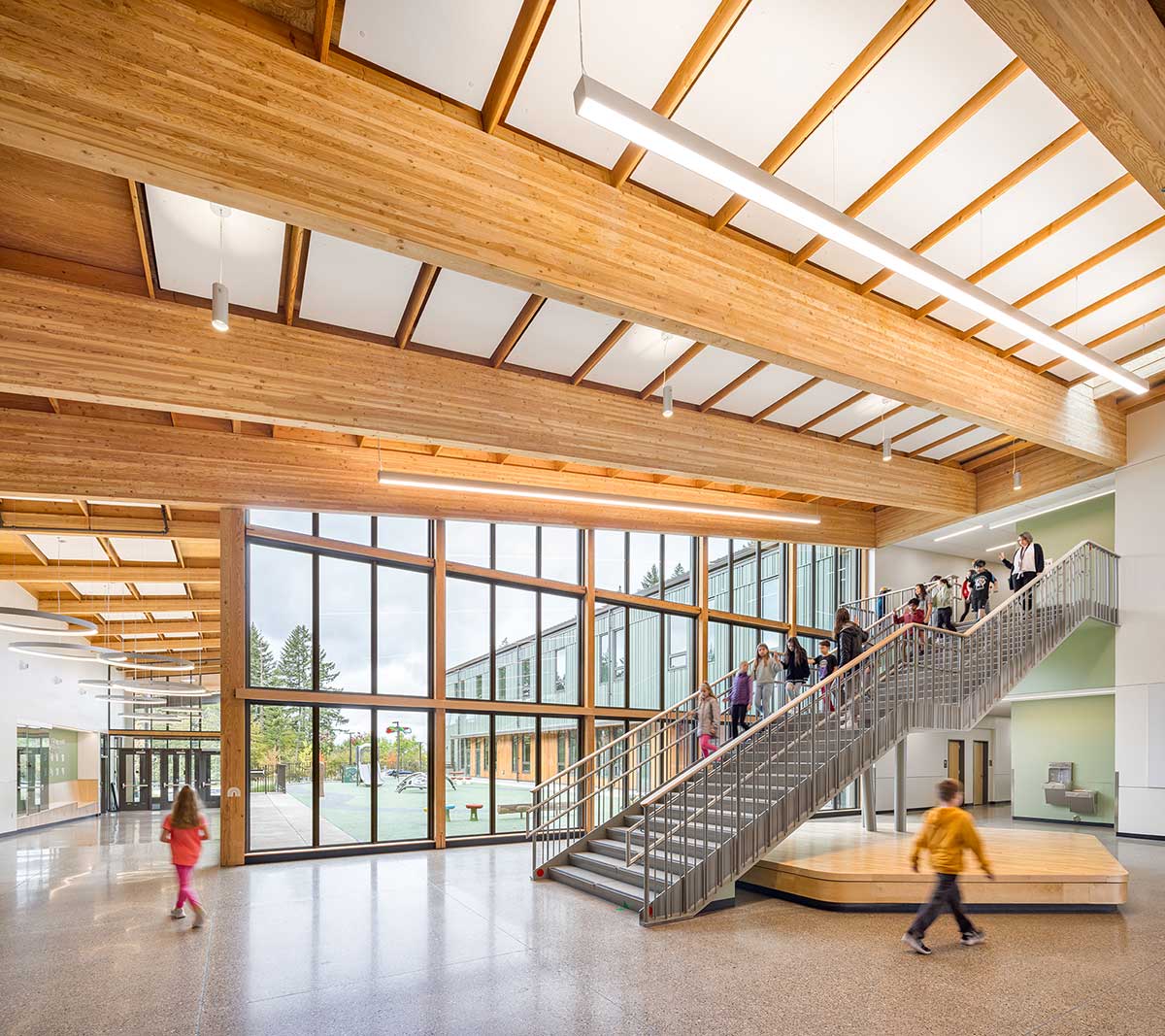
- Seasonal Considerations: Glare may become a larger issue in the winter when the angle of the sun is at its lowest, and so sheer and/or blackout window shades can help minimize glare. These shades can be controlled manually or may be electrically powered and controlled in tune with the lighting control system.
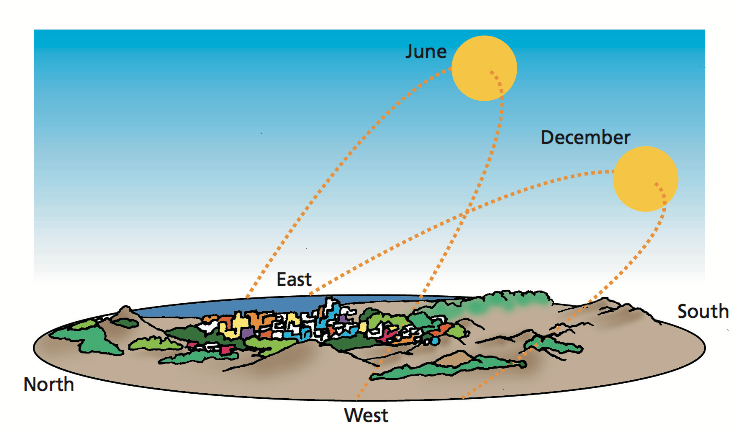
Like these examples, there are many other factors to consider making it crucial for all parties to work together to come up with an effective daylight design strategy.
The color temperature that we get from our electric lights is often fixed, which differs from the dynamic nature of daylight. *White color tuning (also called tunable white or dynamic white) alters the intensity and spectral content of light to change the color from warm to neutral to cool in appearance. This can stimulate or suppress the secretion of melatonin, which impacts our mood, alertness, and overall health. Typically, we want our electric light to mimic the sun as much as possible. But given that the day-to-day activity in a K-12 space often extends well into the late afternoon, we may find it effective to vary color temperature a bit to have extended hours of alertness.
Picking out electric lights is more than just about aesthetics. We generally want our luminaires to blend into and compliment the architectural design. In learning environments, we operate under the guiding principle of “less visual noise, the better.” Lighting in a classroom setting should be integral to and balanced within the architecture, with the goal of achieving a uniform, glare-free experience. In some cases, though, we instead want to showcase our lighting as feature pieces and create “wow” moments. In yet other instances, the two can go together. Lighting can enhance what is already a wow moment architecturally.
A section on lighting design strategies would never be complete without a note about safety. Lighting has been and will continue to be used to make building exits obvious and easy to find, to enhance wayfinding of other spaces, and to make our building occupants feel safe.
Lighting Design Strategies & Incentives
Classrooms benefit from having less visual noise and more uniformity – essentially less distraction. One common lighting design strategy is incorporating indirect/direct lighting from suspended linear fixtures.
Luminaires like the ones above should have a low Unified Glare Rating, a common measure of potential discomfort glare experienced by an occupant. Teaching walls sometimes want more light from a dedicated light fixture, but it becomes important to position these lights to avoid glare, especially if the teaching wall includes reflective whiteboards. Some classrooms in K-6 schools might have a “chill-out zone”, which allows for a bit more play from a decorative light fixture standpoint. Incorporating white color tuning can also be an added benefit.
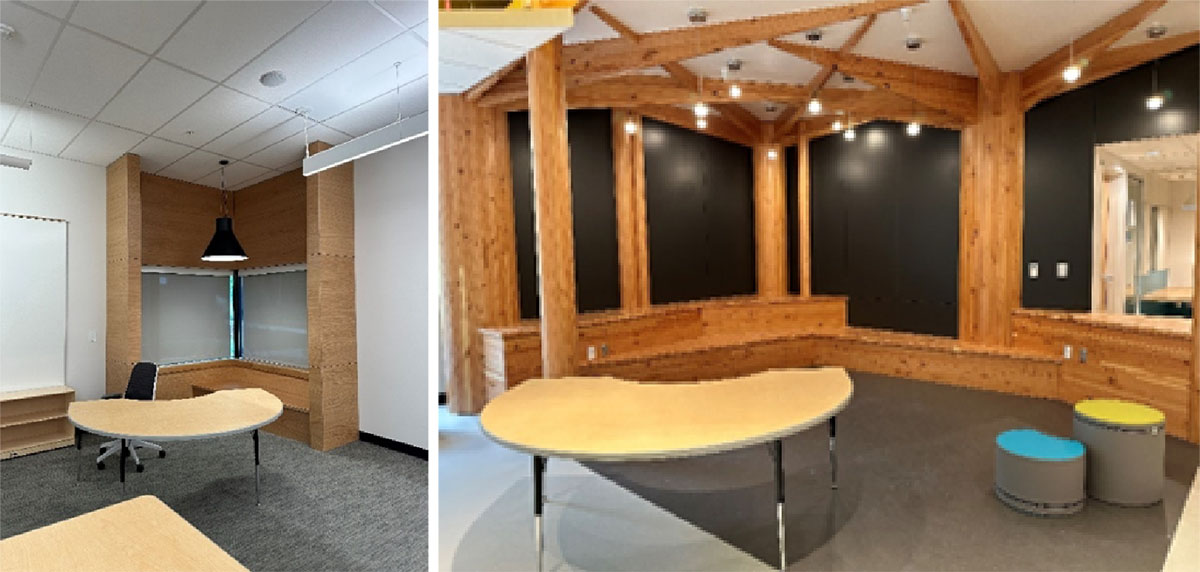
Extended learning areas, often located adjacent to classrooms, create opportunities to change up the design scheme making it more playful or fun. One recommended strategy that Glumac focuses on is biophilic design, which is the practice of bringing elements of nature into the built environment, and making lighting a key component to complement the design.
Sensory rooms and quiet rooms seek to silence and calm the minds of all students, not just students with a learning disability. Changes to environmental conditions can benefit all students and have a big impact on their well-being. White color tuning, RGBW color tuning, and dim-to-warm lighting are additional tools that can be used by teachers for this benefit.
Lab spaces often have stringent light level requirements and there may be other safety and cleanliness concerns to adhere to depending on the programming of these spaces.
Corridors can be more practical with simple lights (downlights, architectural troffers, recessed linear) uniformly spaced, or have these same simple lights arranged randomly for more visual variety. Oftentimes, major MEP systems are routed in these corridors, creating a lower ceiling height, constricting the design a bit. Therefore, what’s happening at the walls (lockers, art displays, etc.), can help broaden the lighting design.
Commons often incorporates lots of daylight with much higher ceiling heights. These spaces are a great opportunity to incorporate larger-scale luminaires to create more interest and wow moments.
Site and exterior lighting’s main goal is safety. The lighting should emphasize the building architecture and be effective for any areas used after-hours (i.e. greenhouses, agricultural sheds, etc.). Local municipal codes will often have strict requirements to eliminate light pollution and light trespass. Generally, shielded light fixtures should be used and uplight should be avoided where it cannot be contained with an overhang or eave.
Utility companies offer many incentives when it comes to lighting. Incentives may come in the form of a $/kWh for conservation actions such as retrofit LED lighting or new LED lighting altogether. These incentives are sometimes very easy to achieve with all lighting specified these days being LED lighting. Eligible rebate programs might also include installing occupancy sensors and lighting controls – things we should be doing anyways to meet energy code.
Tomorrow
The schools we’re designing today will be occupied tomorrow and beyond. We want these buildings to foster a learning environment in which our students and teachers can thrive. Reflecting on the wordplay at the beginning of this article, these elements are demonstrated in each space type we’re designing, with the main theme of “daylight” being displayed throughout.
Lighting design fundamentals used in conjunction with what we’re learning about daylight and lighting control technologies makes for a powerful model. The theme of learning needs to not only be emphasized in our schools but for designers as well to continue to illuminate our K-12 schools for a better tomorrow.
Glumac’s Building Sciences Group is actively working on campus-scale decarbonization framework projects for California State University, University of Colorado, Boulder, George Mason University, and others. With this depth of experience, and the watershed moment of 2030 fast approaching, we caught up with our Senior Sustainability Strategist, Ante Vulin, to discuss the value-add of these projects for building portfolio owners, and what success looks like for a decarbonization project.
Operationally, what does success look like in this space?
For a university that wants to feel like it’s making progress on decarbonization, you should feel confident that your buildings are operating efficiently, meaning you know how much energy they’re using, and you have the know-how on your staff to be able to identify and rectify problems as they pop up.
It means that as you’re developing new capital projects or new renovations or any project where you’re touching your physical plant, you have an idea of where you need to be in terms of performance of those systems, of the types of technology you’re going to deploy and how you’re going to future-proof that equipment.
So, it’s not just the state we’re going to work in today, but it’s going to work in the future in a changing climate or in a changing code environment.
University campuses run the gamut of building types: residential, labs, data centers, entertainment venues, etc. So how do you meet the challenge of balancing all of these major usage variables in a single plan?
It’s definitely a challenge to balance a lot of different building types and especially on a university campus where you have different schedules, different research needs, different end user groups who have different needs or be more or less vocal about wanting changes done to their facilities.
We like to use data to help simplify the process to identify what are your biggest emitters or where are your biggest opportunities for operating cost reduction. That lets us focus our attention there first before we tackle everything else.
The phrase sometimes is “Eating the elephant one piece at a time.” And in this case, we know the pieces that make sense to eat first or the things that are going to save you the most money in the long term. Then once we focus on those metrics that are really data-driven, we can also talk about the qualitative metrics.
What are the academic or research or pedagogical needs where you want a building that embodies what you are striving to at your university and then set the last point is how do you resonate with what people care about? We hear from when we do surveys on university campuses that food is really important. And as engineers, we may not be the experts on food, but we know how to tie that into your carbon story and your sustainability story and find those opportunities even if your other major capital project budget is all tied up.
How would we help tell that story for a university? People see Glumac as an engineering firm. So if we’re talking about carbon impact of the food we have on campus, our clients might ask: What does that have to do with the HVAC system?
Well, our real strength at Glumac is we can talk to you in a quantitative and qualitative way about the relative impacts of these different metrics, whether it’s staff or student commuting versus your buildings versus all the things you buy, versus the impact of the certain community your institution happens to be located in. And by bringing numbers into this conversation, I think it helps prevent that analysis paralysis where you don’t know where to start, where you know certain things are important, but you may not have much control over them.
Or you sometimes feel you have competing opportunities where, say, you’re an institution that is focused on serving a diverse community that often includes a heavy amount of commuter students, you don’t want to get rid of that opportunity where people are living at home or in lower cost situations and force them to live in brand new campus housing. That kind of conflicts with your mission.
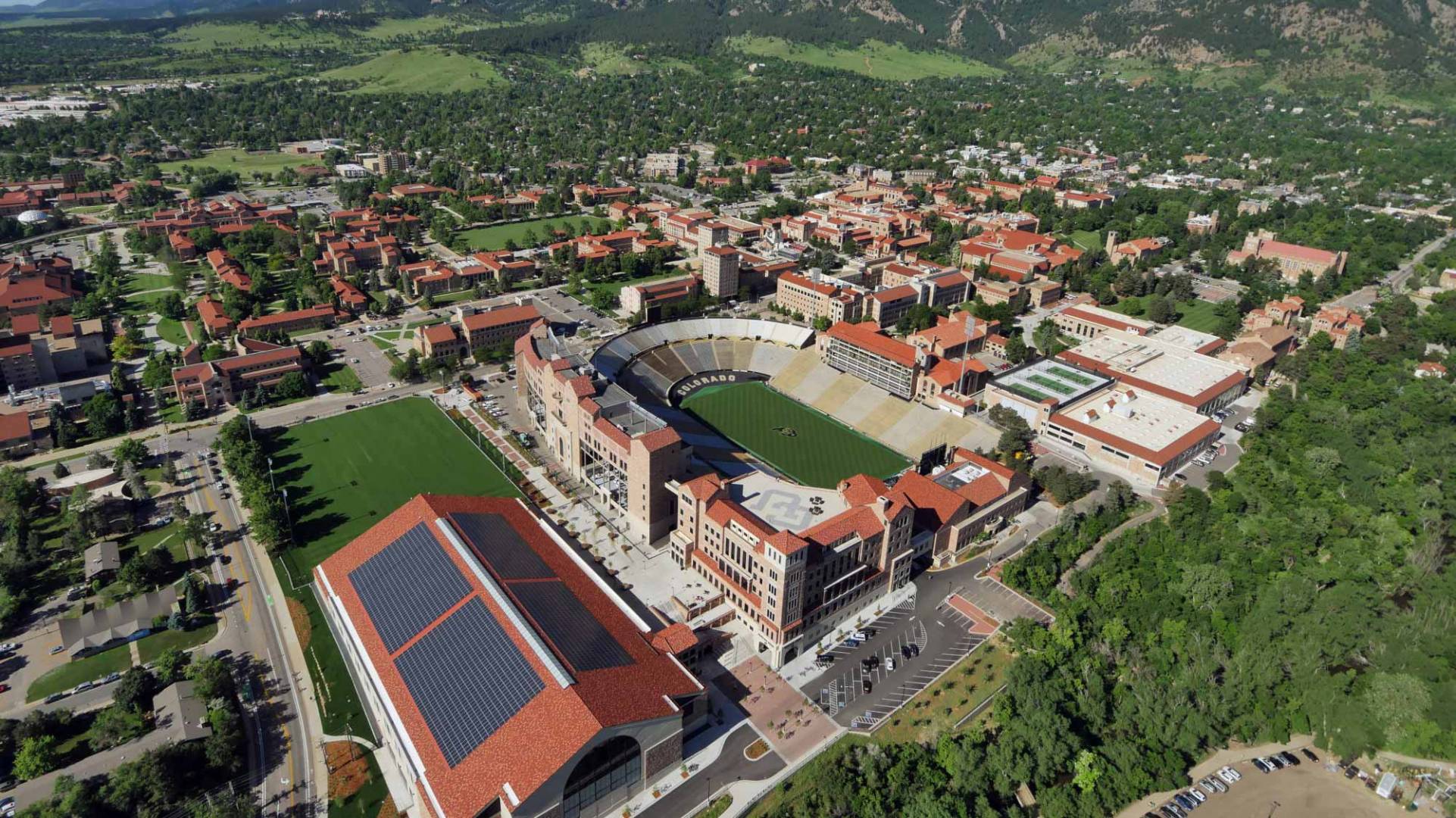
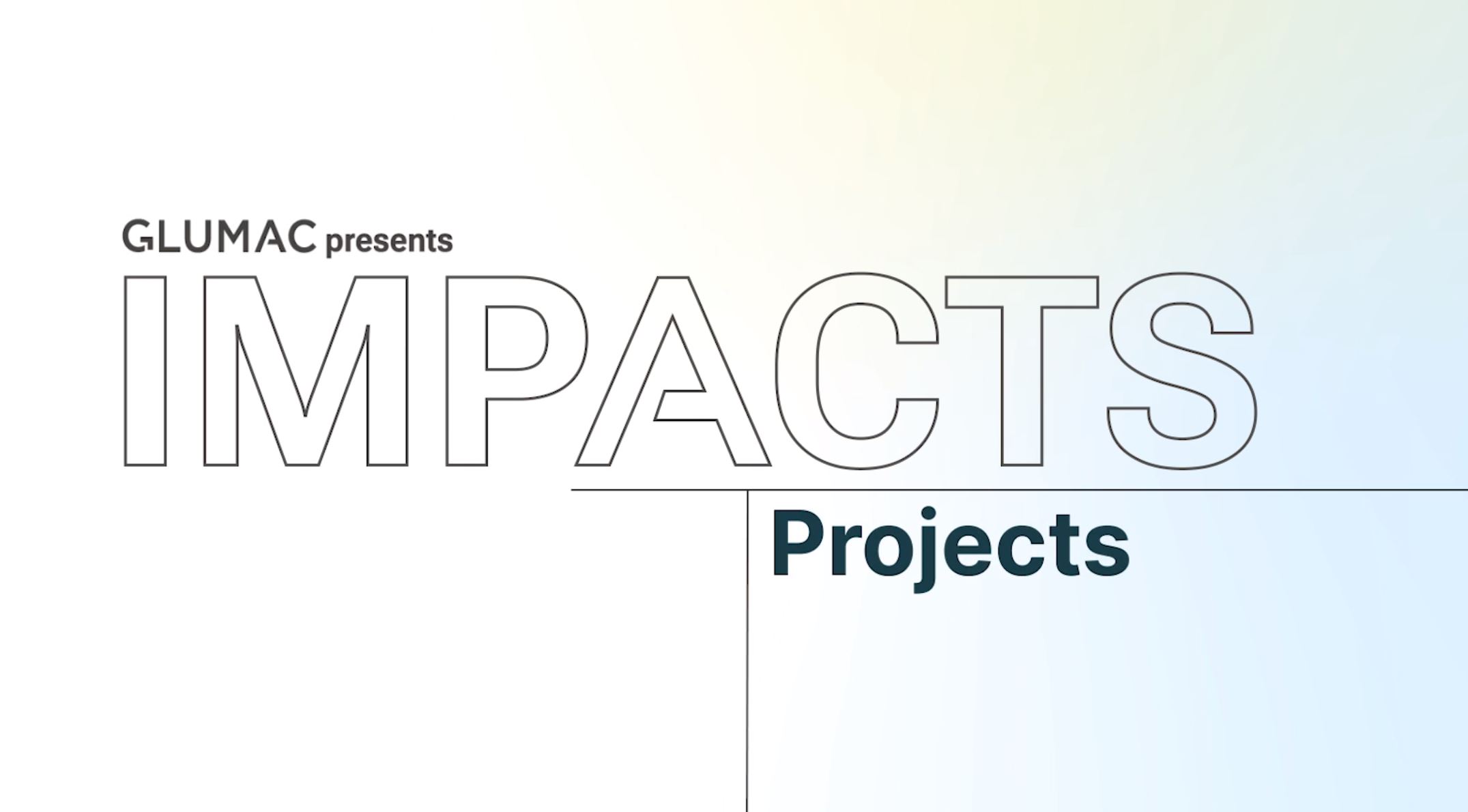
Learn about our decarbonization study at the University of Colorado, Boulder
What a decarbonization plan can do is lay out for multiple stakeholders how this whole path as we draw emissions down to 0, what’s the right order? And it’s not saying we’re not going to take any action on commuting right now, but it’s more about documenting the actions that the university could take. So, for example, how is the university interacting with the local or regional transit agencies? What are the opportunities there, perhaps more in an advocacy role, And that starts to move the needle on the commuting side. While in the same time, the things that the university does control, like its physical plant or its capital planning project are also making deep gains on the emissions that are directly under its control. That’s the win/win that we try to find.
What is the primary challenge to success?
I think the challenge, at a high-level, is limited resources and those resources include money, time, staff capacity or expertise. And that that balance will be slightly different for every institution.
What we try to bring is that quantitative method of understanding, OK, within these constraints, what are my lowest cost or fastest or easiest solutions that still lead to big emissions reductions.
The slight upside of where we are right now in that climate reduction path is there are still a lot of low hanging fruit. We’ve seen many universities roll out LED retrofits as one kind of low hanging fruit that they’ve solved. So after that, let’s dig a little deeper. Smart heat pump deployment, deploying electric vehicles and fleet electrification in a smart way as well as data-driven monitoring of existing buildings. How do we actually ensure what we have is operating as efficiently as possible? I think those are those key steps that we can all take right now. They’re going to huge gains and set us up for more success with those harder to, to realize gains down the road.
2030 has long been shorthand for a necessary point where sea change regarding climate is necessary. What do you want to see happening in a built environment then?
2030 is really the milepost on the way to 2050 where science tells us we need to draw down operating carbon emissions to zero. By 2030, what we need to see happen for all our buildings is that the new buildings should be at a net zero level of performance. And that means they should be very efficient. They should be using heat pumps, they should be running on electricity.
And that needs to be paired with a renewable energy strategy. So that means whether it’s on site building integrated renewables or having an off-site renewable strategy that’s harnessing say the larger purchasing power of a university, we need to be all our new buildings to be operating that level where they are not adding operational carbon emissions to a university’s footprint.
For existing buildings by 2030, we need to know everything that we have in our buildings that’s polluting and know when it needs to be replaced so we can make that smart, most cost effective end of life transition to all electric equipment.
And then we just need the data. For most universities, addressing those items gets you through a huge percentage of your missions. If you can do that, you’re in great shape. And then we need to have the data that starts guiding us towards those harder to control things like car and electric vehicle transition, purchasing those factors that are less directly in your control. But you’re going to need to start making some investments to help get you to that path.
As the U.S. building stock continues to grow, so do the risks of climate impact.
As “Engineers for a Sustainable Future,” we understand that technological advancements are forging a clean and resilient future at a pace never seen. And we understand that we are exceptionally positioned to have a measurable impact on carbon reductions through our innovative engineering and consulting.
Now is the time to take a larger share of our projects beyond code and take a holistic look at carbon and human health for all. Codes are ramping up, governments are implementing new policy, and climate change continues to threaten our health and livelihood.
To stay ahead of the market change and adapt to new climate conditions, we need to make deep energy and carbon reductions a best practice on our projects. And we need to prove performance through transparent building reporting and measurable, improved progress.
This is why Glumac’s Executive Leadership, Engineering Services, and Building Sciences Groups came together to develop our Climate Commitment Action Plan. In it you’ll find concrete steps we’re taking for achieving our AIA 2030 and Carbon Leadership Forum MEP 2040 commitments, improving our design processes, and industry outreach and advocacy we undertake.
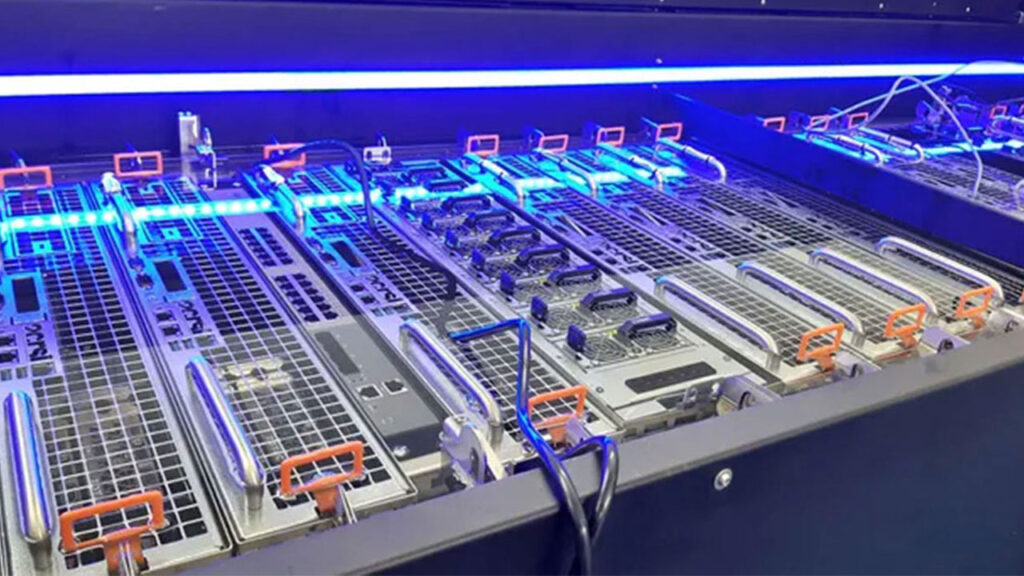
The next generation of high-powered AI servers are becoming commonplace in data centers to accommodate increasing AI use across many industries. Pushing the bounds of computational power comes at a cost: increasing power consumption.
The liquid-cooled servers needed to power AI computing will need to work alongside air-cooled IT equipment, leading to a hybrid environment. Direct-to-chip and immersion cooling provide great opportunities for increased heat rejection efficiencies and better parameters for heat reuse. Liquid cooling of AI servers does not require a fundamental change to facility water systems, but the cooling systems will need to evolve to support both liquid- and air-cooled requirements that will exist in a hybrid environment.
Today, new liquid-cooled data centers are being designed and constructed globally to support the new 2.7 kilowatts (kW) NVIDIA Blackwell GB200 GPU and the new 97.2 kW NVL72 liquid-cooled servers. The increased power demand of AI should also drive the development of renewable and low-carbon technologies to meet decarbonization targets. Data center developments will need to focus on increased usage efficiencies and delivering effective heat reuse.
We worked with our partners in the Tetra Tech High Performance Buildings Group on its latest white paper, “Taking the Heat Out of AI: Sustainable Solutions for Liquid-Cooled AI Data Centers,” discusses challenges and sustainable solutions of designing for this new technology.
Image courtesy of Submer
In 2018, Glumac began work on a strategic road map for the California State University system that supports decarbonization efforts across its 23 campuses. With the overall of providing a pathway to carbon neutrality, this design standard provides guidelines for the university and its staff to decarbonize the operation of all its facilities.
Since then, we’ve grown this portfolio of work across the US, including work with the University of Colorado, Boulder, and George Mason University.
We sat down with Reese Netro, a sustainability strategist with Glumac, to learn more about what exactly goes in to decarbonizing an entire university system.
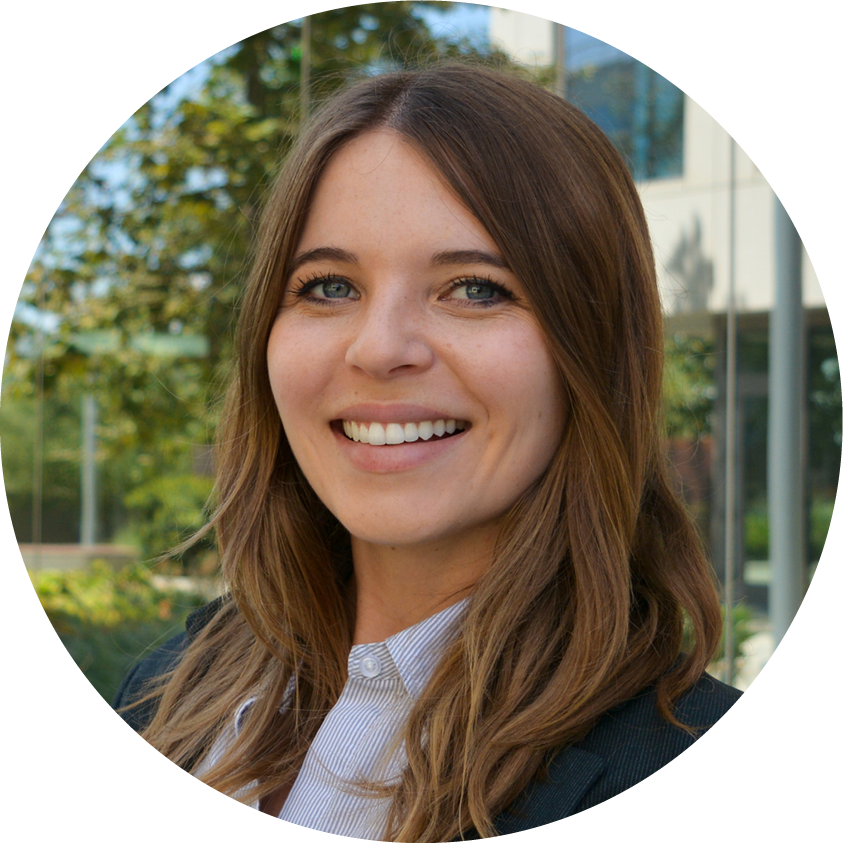
Reese Netro | Glumac
As Sustainability Strategist at Glumac, Reese supports USGBC LEED, Living Building Challenge, WELL, and Fitwel green building certifications from initial to final stages. She also works to integrate sustainability strategies on projects in collaboration with interdepartmental staff.
Nvidia’s groundbreaking H200 GPU chip is setting new standards with double the speed of its predecessor, the H100. This unparalleled performance upgrade, however, forces designers to grapple with a considerable increased energy demand.
The data center world, which collectively contributes nearly 4% to global energy consumption, currently relies heavily on air cooling. Enter forward-thinking solutions such as evaporative cooling, which presents as much as a 20% reduction in energy usage. Yet, this energy-conscious approach brings about its own challenge – a massive amount of water consumption.
Anticipating a greener future, data center design is pivoting toward liquid-cooled server technology. Liquid-cooled AI servers, boasting a capability of a billion calculations per second, could mark a monumental leap forward in sustainable technological advancement. Join us in an exclusive webinar where we venture into the intricate landscape of AI data centers.
In our latest webinar, we’re joined by Dave Martinez of Sandia Labs and Steve Harrington of Chilldyne to unravel this tapestry of technological advancements, navigate environmental considerations, and explore collaborative solutions shaping the sustainable future at the intersection of AI and data centers.
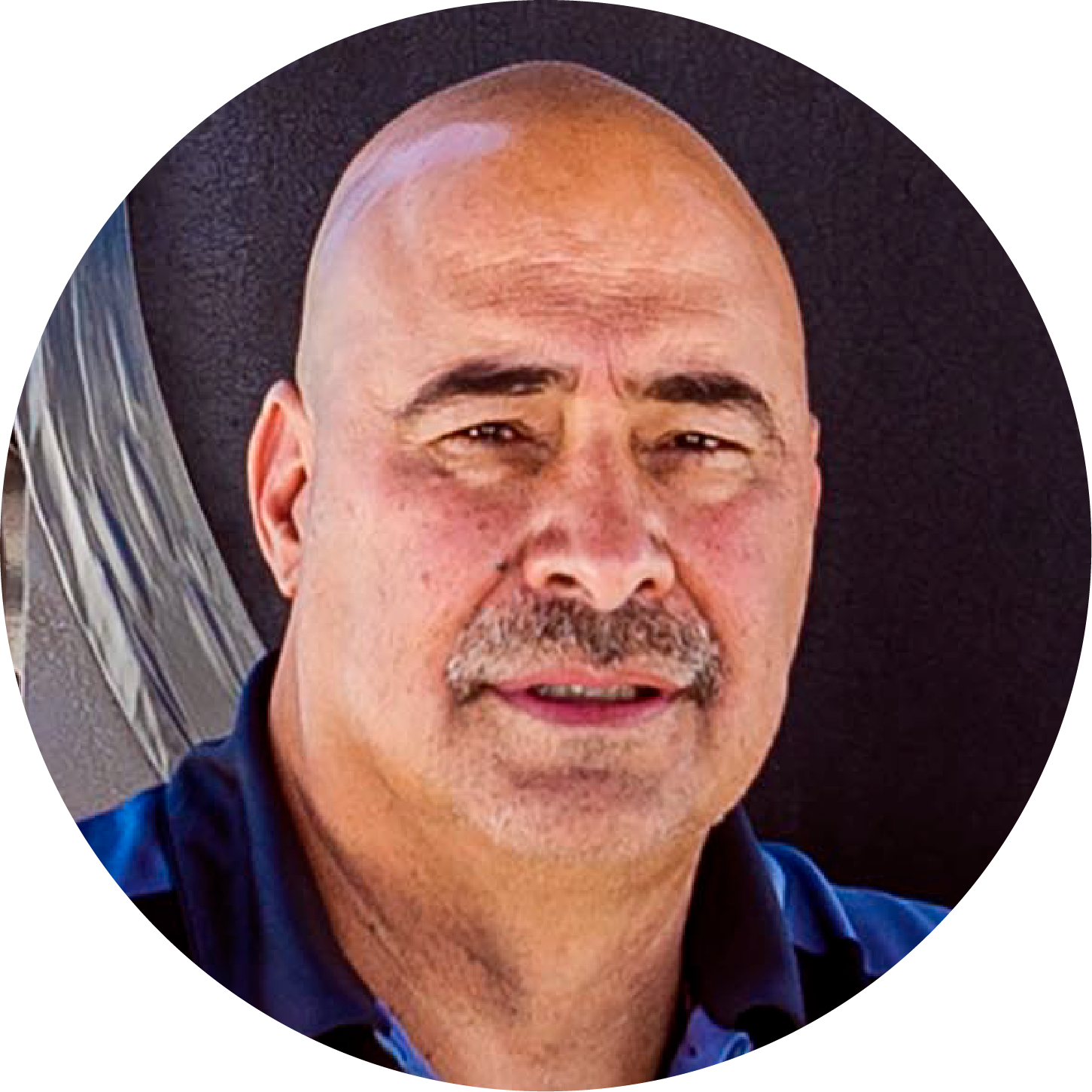
Dave Martinez | Sandia National Labs
David Martinez is the Engineering Program Project lead at Sandia National Labs Corporate Computing Facilities (CCF). David has in depth understanding of HVAC controls, IT, Facility hardware implementations, and is widely viewed as a DOE resource for both air and liquid cooled data center deployments.
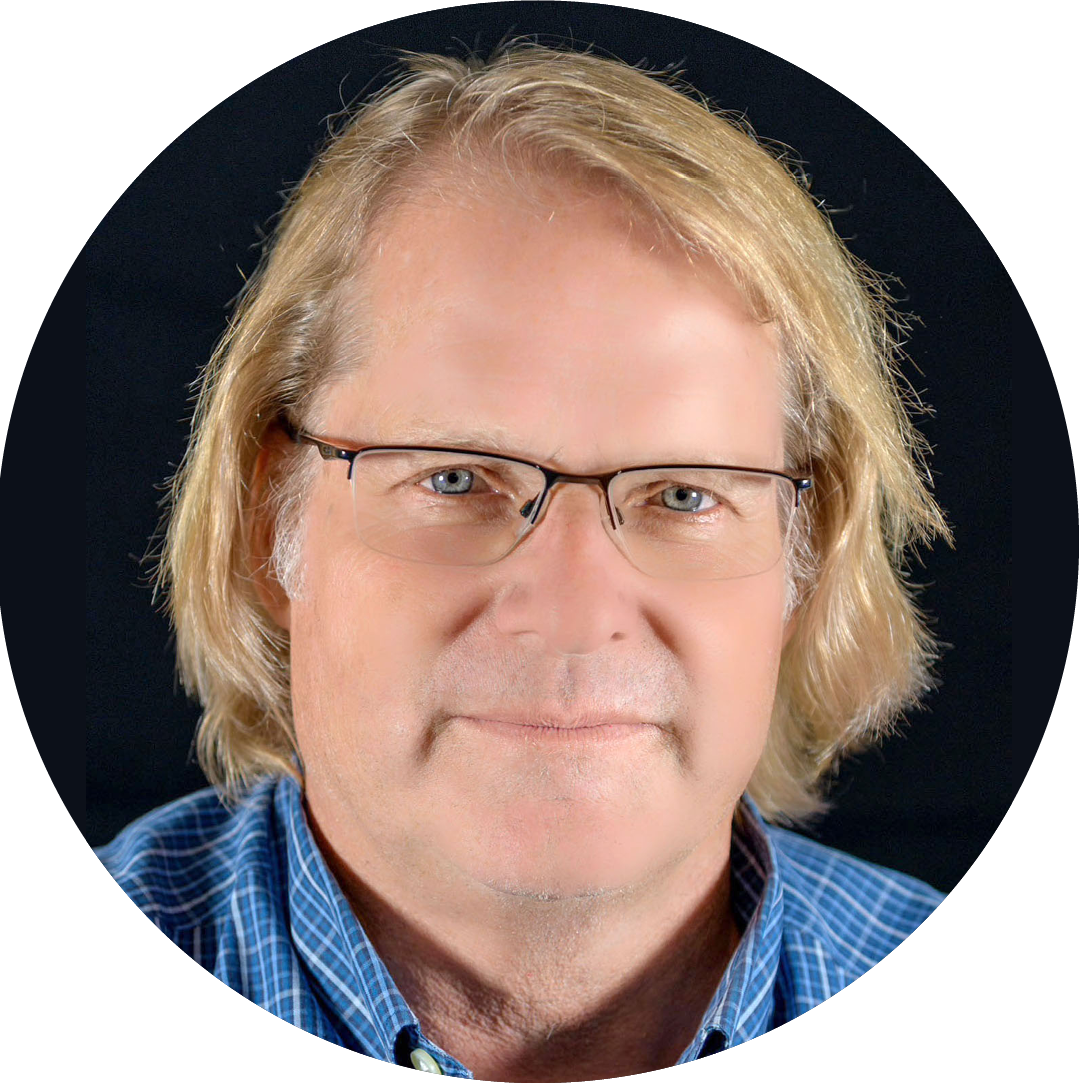
Dr. Steve Harrington | Chilldyne
In 2011, Dr. Harrington founded Chilldyne to bring his engineering, fluid dynamics, and electronics cooling expertise to the data center. His personal goal is to reduce energy consumption and the carbon impact of data centers globally by deploying liquid cooling to as many servers as possible through widespread adoption of liquid cooling .
Recently, Michael Adams of Glumac’s Energy team sat down with HMC Architects to discuss the impacts of Title 24 code updates on the design of education spaces. His interview is reproduced here with HMC’s permission.
Every three years, the California Energy Commission (CEC) updates its section of the Building Standards Code, Title 24 Part 6 – California Energy Code, by working with stakeholders in a public and transparent process. The updated 2022 Code took effect on January 1, 2023. The goal is to improve efficiency and reduce emissions from California homes and businesses, which represent 70 percent of the state’s electricity use and are responsible for a quarter of the state’s greenhouse gas emissions.
Nationally, California is a leader in environmental standards, and Title 24 is one of the tools state leaders use to push the envelope. The Title 24 Building Standards Code dates back to 1978, when previously disjointed building regulations were unified, covering all aspects of building construction. As climate change and greenhouse gas emissions have become pressing issues, energy use and emissions standards have become more critical.
As we adopt the 2022 code, there are several changes school districts, architects, and engineers need to understand better. We talked with Michael Adams, CEA, LEED AP BD+C, to get answers and some perspective. Michael is an associate and senior energy analyst at Glumac; a global engineering firm focused on creating sustainable, resilient buildings that provide healthy, productive, and equitable spaces for all communities. Glumac is an engineering partner on many HMC projects.
What are the noteworthy changes to the Title 24 energy code?
One of the significant changes is a prescriptive requirement for solar photovoltaic and battery storage systems for most non-residential new construction building types (Section 140.10). The amounts are based on a project’s conditioned square footage or available roof area (calculated as Solar Access Roof Area – SARA). Although a prescriptive requirement only, it will make it difficult for applicable buildings to meet Title 24 compliance via the performance approach without any renewable/battery storage systems in their design.
For non-residential projects, there are various improvements to performance requirements for the envelope, mechanical, lighting, and plumbing systems. A few of the more notable changes include:
- Increased prescriptive insulation requirements on metal-framed exterior walls
- High prescriptive glazing performance (U-Value and SHGC) with new climatezone-specific requirements
- Reduced prescriptive lighting power density (LPD) requirements
- Increased mandatory mechanical system efficiencies
- Increased prescriptive requirements on airside economizers on smaller systems (some exceptions)
- Prescriptive mechanical system type requirements (heat-pump based) for some program and building types
- High mandatory insulation performance requirements for envelope systems in alteration/addition projects
What are the impacts and cost implications of the updated energy regulations?
The photovoltaic/battery and higher performance standards requirements will increase first costs (the initial cost to construct). We expect that there will be lower energy use intensity (EUI), lower greenhouse gas emissions, and lower utility bills throughout the life of the building.
Additionally, these code changes will push more projects to consider energy use holistically, modeling actual predicted energy use rather than checking the boxes on a list of different components that must meet minimum requirements. This will require an increased understanding and knowledge of the Title 24 Part 6 energy code.
Read More at hmcarchitects.com
Indoor air quality has a major role to play in resilient building design. As the COVID-19 pandemic and the growing presence of climate-related disasters converged in recent years, the need for our indoor spaces to keep us safe, together, and working has become more apparent than ever. Recently, we were joined by Dr. William Bahnfleth of Penn State University for a discussion digging into ASHARE’s groundbreaking new Standard 241, which addresses these issues head on. Dr. Bahnfleth shares insights drawn from helping develop the standard and illustrates its potential to create built environments that are safer and more resilient to a changing climate.
On the webinar below, you’ll also hear from Chris Rush of our partner firm Hoare Lea. An expert in indoor air quality, Chris provides a guide for making resilience a reality on our projects. And lastly, Erik Malmstrom of SafeTraces provides a look at how their technology helps us quantify the impacts of healthy building design, to ensure design intent becomes reality.
Presenters

Dr. William Bahnfleth | Penn State University
Dr. Bahnfleth is a Fellow of ASHRAE, the American Society of Mechanical Engineers, and the International Society for Indoor Air Quality and Climate. Dr. Bahnfleth is the author or co-author of more than 170 journal articles and 14 books/book chapters.
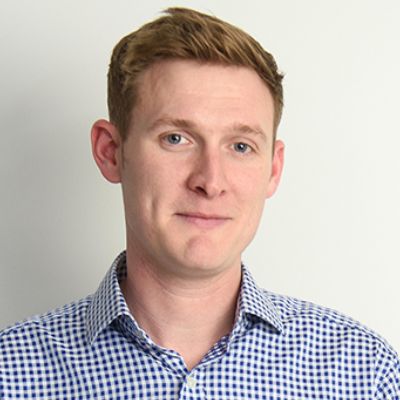
Chris Rush | Hoare Lea
As Air Quality Group lead at Hoare Lea, Chris focuses on promoting the crucial role indoor air quality plays for our health and wellbeing, and examines the opportunity buildings play in delivering better health outcomes for occupants.
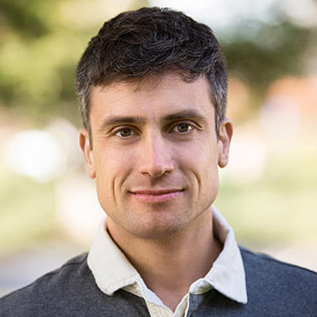
Erik Malmstrom | SafeTraces
The CEO of SafeTraces, a Bay Area-based technology company and leader in DNA‑enabled diagnostic solutions for indoor air safety, Erik is a successful and experienced thought leader driven to create a better, safer, more sustainable world.
We’ve discussed building embodied carbon a lot at Glumac, stating its overall necessity as part of a global carbon drawdown, strategies for reducing it in new buildings, and even the impact material choices have on a building’s life-long carbon footprint.
And that materials challenge looms large. Though many manufacturers still do not disclose the embodied carbon of their products, the most progressive manufacturers that supply the major materials buildings use – concrete, steel, and wood – is where the lion’s share of good data lies, and where the focus of our work is with our clients. But even so, it is difficult to make building specifications meaningful because with the lack of data, you run the risk of being too aggressive, or too lax, because materials are regionally and market sector sensitive.
Senior Sustainability Strategist Ante Vulin provides context into the global impacts of a building’s embodied carbon.
So where can we work and have the most impact under these conditions? The answer may be large-scale adaptive reuse. There is a big opportunity in front of building designers to avoid carbon emissions by making our existing building stock a larger part of the climate solution.
We recently had the pleasure of working with the State of California’s Department of General Services on its Resources Building Renovation in Sacramento. As part of the of this renovation of this 652,000-square-foot building, the steel structure, and steel deck and concrete floors will be retained. The structural reuse alone reduces its embodied carbon intensity by 65% over typical new construction. This demonstrates the power of reusing existing buildings in avoiding carbon emissions on a large scale, as there is so much embodied carbon tied up in the production and delivery of concrete and steel.
Chief Sustainability Strategist Nicole Isle diagrams carbon savings through adaptive reuse.
What about new construction?
Inroads to carbon reduction through smart material choices can still be made for new construction projects. The structural strategies available to reduce embodied carbon are simple, can be cost neutral, and the amount of good data available for market ready alternatives is most robust for these materials. For example, the all-new Clifford L. Allenby building achieved a 15% reduction in embodied carbon of the entire structure and envelope through the concrete mix alone.
This Sankey flow diagram is a model output of a new construction office building we are currently working on. On the left side, it shows the materials with the highest potential to reduce embodied carbon. Again, concrete and steel are the biggest culprits by volume. And looking all the way to the right, market ready low carbon alternatives can potentially reduce the embodied carbon of this building by 35%.
The potential is growing for carbon reduction across building market sectors. Let’s chat about your next building, campus, or real estate carbon reduction project!
This post was made in part of a series along side our partners in Tetra Tech’s High Performance Buildings Group.
You can read the rest of the group’s posts here.
COP27 is focused on action this year. As global leaders gather, the priorities to are twofold: accountability, and; solutions to implement now.
Accountability
Loss and damage negotiations are taking centerstage. Negotiations on how much nations should pay in loss and damages is an important topic, as well as the assistance needed to help the poorest countries transition to renewable energy. These conversations are timely with the re-entry of oil and gas companies, which were banned from COP last year. Given their record profits, largely due to the Ukraine crisis, leaders are pressing for a windfall tax to shift profits to aid global inequities, while acknowledging it’s time for governments to deliver on climate finance commitments.
Solutions
COP27’s Decarbonization Day focused on technologies that are emerging as potential solutions to help nations achieve their Nationally Determined Contributions (NDCs), and businesses to achieve their climate goals. The day provided an opportunity to discuss approaches and policies and showcase technologies that facilitate the transition towards a low carbon economy.
Discussions trended toward decarbonizing high-emitting sectors, namely oil, gas, steel and cement, which represent more than a quarter of global CO2 emissions. American President, Joe Biden, rallied 122 countries to join the Global Methane Pledge, aiming to reduce emissions by 30% by 2030.
In oil and gas, the following was explored:
- best practices to end methane venting and flaring and cut methane leaks in operations
- methods to improve energy efficiency, use renewable power and Carbon Capture, Utilization and Storage (CCUS).
Further topics included low carbon steel and cement and adopting circular economy approaches to reduce needs for new materials, while recognizing the importance of these products for improving infrastructure in developing nations across Africa and the Global South.
The ‘Breakthrough Agenda’
Nations representing over half the world’s GDP, including the United States and the United Kingdom, unveiled a one-year plan with 25 collaborative actions to be delivered by #COP28 to help make clean technologies cheaper and more accessible everywhere.
“Fossil fuels are a dead end. We need to increase renewable energy deployment to around 60% of total energy capacity over the course of the next eight years, which means roughly a tripling of install capacity over the course of this decade.” United Nations Chief António Guterres has said.
And, as the UN expressed in an article last week, this is more than possible, because the world has tripled its renewable energy capacity over the last decade. We just need to do it again, as Guterres has expressed: “The technologies are there, the finance is there. It just needs to be deployed in the right place, where the emissions are and where the population growth and energy demand is.”
The climate provisions in the recently passed Inflation Reduction Act (IRA) are substantial. The sustainable design community’s advocacy efforts and demonstrated projects promoting efficient, low carbon, resilient and healthy buildings has finally manifested into U.S. policy creating new climate funding resources and extending existing programs. For a quick understanding of IRA’s climate provisions, we like this USGBC summary.
At Glumac, we helped design the largest net zero government office in California, demonstrated the sustainable ROI in developer lead projects in Texas, and improved the resilience of the Oregon State government. And, there is a rise in climate action from campuses and governments as our work on building and transportation decarbonization and clean energy plans continues to grow. Looking ahead, we are anxious to see how this new climate funding spurs broader market uptake especially at scale with the larger building portfolio owners.
Glumac’s Building Sciences Group, made up of our sustainability, energy, and commissioning experts, is leading the charge informing our MEP staff and our clients on the benefits of the new legislation. Looking ahead, we’re confident that the rapidly growing number of requests we are receiving for efficient and low carbon buildings, new and existing, will continue.
The bill is meant to put the U.S. on the path to reduce GHG’s 40% by 2030 and make energy efficiency and clean energy increasingly more cost effective year after year. What’s more, the IRA will undoubtedly sweeten the ROI for smart, sustainable buildings. We are thrilled by this massive boost in federal support and we have a renewed sense of purpose and pride in the work we do alongside our client owners, developers, and design partners. Let’s keep going!
For our latest installment in our Data-Driven Design Series, we spoke with Jon Robertson, Glumac’s Lone Star Region Plumbing Manager, about strategies for reaching net zero water and how we’re improving the water efficiency of our projects.
Water reuse and conservation is a major aspect of resilient design in the face of climate change. In this video, Jon discusses strategies he’s implementing on projects today that are improving the capture and reuse of greywater, the efficiency of systems, and the overall reduction in the waste of potable drinking water.
Visit Glumac’s Vimeo to follow the rest of our Data Driven Design Series.
&nspb
While a lot of attention is paid to the role transportation plays in the massive carbon draw down necessary to mitigate the worst effects of climate change, designers in the built environment actually have a much larger piece of the carbon pie to slice: Building materials.
Expanded public transit and electric vehicles definitely play a role in getting to a net zero future. But globally, vehicle travel accounts for around 6% of yearly global emissions. And air travel accounts for around 2%. In contrast, the production of cement, a key material used in building construction, is responsible for around 5% of global carbon emissions. Likewise, steel is a little over 5% of global carbon emissions. So more than 10% of global emissions each year come from materials that are ubiquitous in the built environment. The good news is that this is fertile ground for making significant carbon reductions in our building projects.
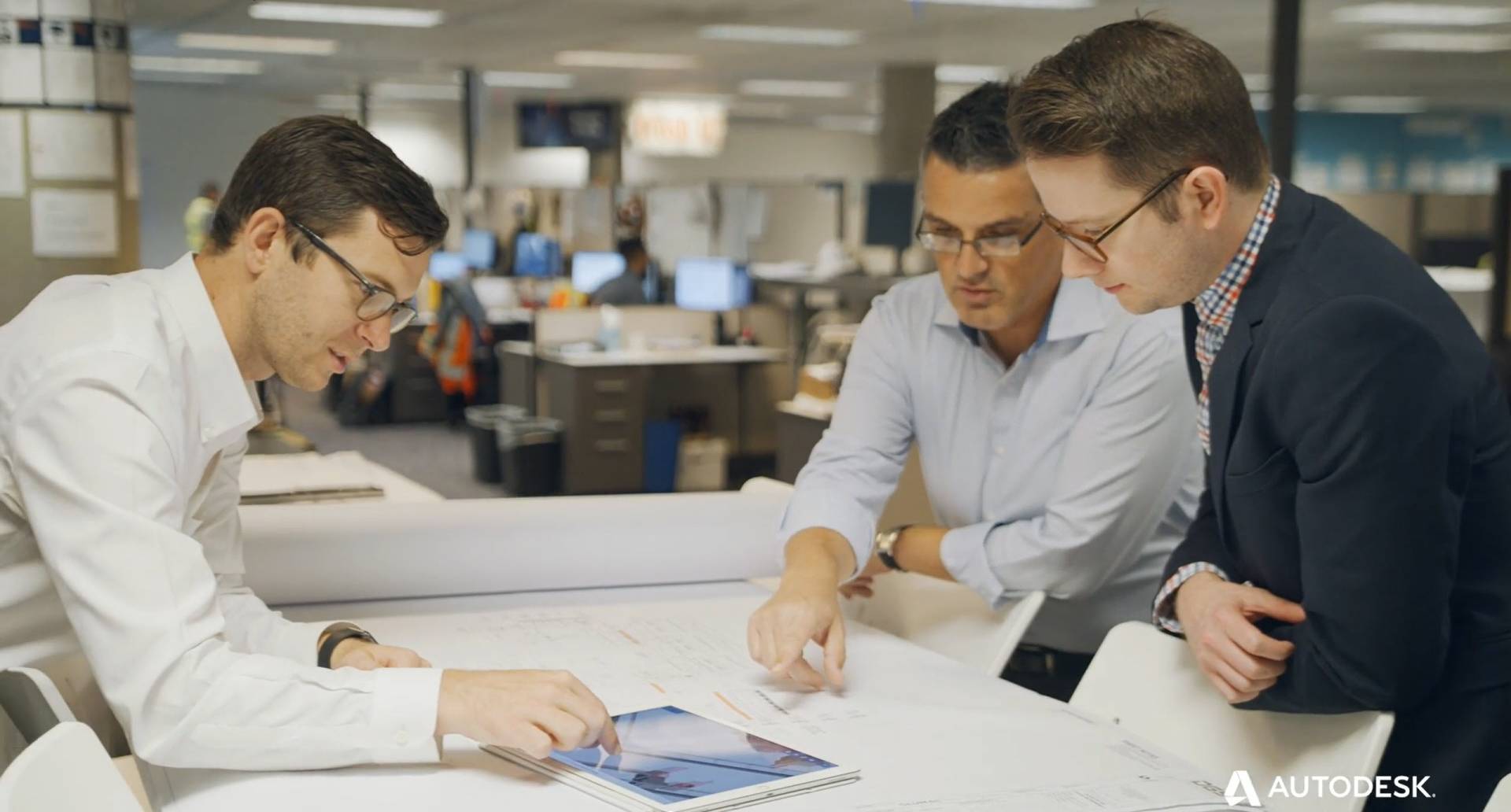
Increasing stakeholder understanding of embodied carbon is another way to help us push the use of low carbon materials in our projects. It probably takes between 15-30 years for the operating emissions of a building to equal its embodied carbon.
We’re already discussing systems electrification as a key to a low carbon future. What’s challenging about these materials, though, is that they’re very hard to electrify. Part of that is pure chemistry. Even in a totally solar powered cement plant, the chemical process of creating cement would still release about half of its current carbon offput into the atmosphere. And manufacturing steel requires extremely high temperatures that are very hard to reach with totally electrified systems.
All these industrial processes inherent in building design and construction make efficiency and informed materials selection even more important in reducing our building’s overall carbon footprint.
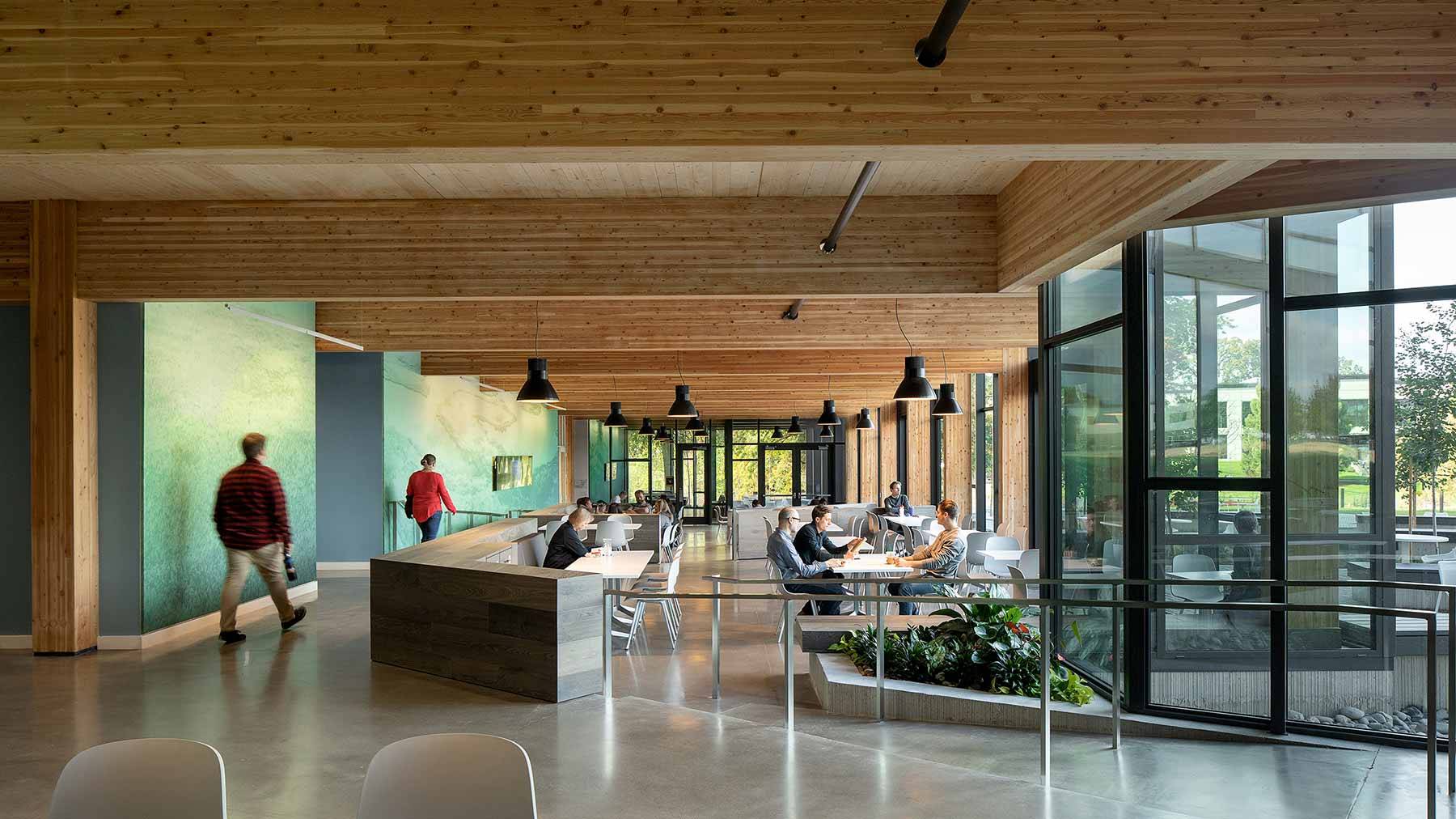
1. They can offer an amenity that is still somewhat scarce across the nation, attracting employees or residents that possess or will possess EV’s.
2. Electrifying a fleet or bus network saves an immense amount on maintenance and gasoline every year.
How do we do it?
When considering materials, just like with energy, we start with efficiency: Using less, and making sure what we do use is being used to its highest value it. And using less material like concrete is something the A/E/C industry is very interested in. From cementless concrete to CLT design, there are a number of affordable options we are pursuing:
- Concrete mixes that reduce cement content – e.g. using fly ash, slag, glass, or even CO2 in place of cement.
- Another reduction option while using concrete involves delaying strength requirement timeline for your concrete so it doesn’t have to be as strong as fast. This can reduce the amount of cement needed, and can lower concrete’s contribution to embodied carbon by as much 30%. That’s a huge relative amount in a building.
- Sourcing steel that’s made from high recycled content. That is nowhere near as carbon intensive as producing steel from ore. Depending on your geographic location, this can be a cost-effective approach.
- Wood is also becoming a popular choice for structural material in large buildings. One method is using cross-laminated timber as decking to replace concrete. And those projects that rely heavily on wood can save as much as 40% of embodied carbon as opposed to a typical concrete structure.
- More structurally efficient systems: Studies show utilizing a slab and beam system over a flat slab system can save 15 – 20% of embodied carbon
These big changes can sometimes cost more money. And there aren’t as many suppliers or contractors who create or work with these materials. But that premium is dropping as industry demand grows. Presently, however, there are scheduling advantages with mass timber specifically that can help create savings. Many mass timber structures can be crane erected with weeks of time savings, and that creates significant cost saving overall for a project.
When we use carbon as a lens to reevaluate business as usual, it presents us with an opportunity to save time, save resources, save money, and hopefully create more beautiful buildings.
Learn more about our Sustainability Group’s approach to reducing carbon in the built environment.
Email Ante Vulin to discuss your building’s carbon needs.
For our latest installment in our Data-Driven Design Series, we spoke with Brian Goldcrump, Glumac’s Northern Region Energy Director, about the impact our power grid has on building decarbonization.
With the recent efforts by states on the West Coast to divorce their energy grid from fossil fuels, building system electrification now presents a real and actionable path toward lowering the operational and embodied carbon of our projects. Brian presents a live dashboard of the power mixes of the West Coast energy grid, and shows how we can help owners, developers, and architects create building systems that are more efficient, effective, and sustainable.
Visit Glumac’s Vimeo to follow the rest of our Data Driven Design Series.
&nspb
Austin, TX, has implemented a series of rebates and guidelines to improve the rainwater harvesting capacities of residential and commercial buildings.
As much as $100,000 is available per project, including $5,000 for rainwater harvesting equipment, and $5,000 to conduct a water efficiency audit. The immediate impacts on a building’s efficiency and performance are obvious, but the long-term savings for owners and developers can be immense, particularly as future water conservation ordinances become more strict.
Water conservation is a key tool in mitigating climate change impacts. Results in states that have offered owners and developers incentives to improve their on-site water reuse have demonstrated positive results in water supply, even in the face of prolonged draughts (something Texas and the South are very familiar with).
Glumac has years of experience developing rainwater harvesting systems across the West Coast, and most recently at the Broadway Office Development in San Antonio. We even developed a rainwater harvesting system for our own Sacramento office!
Read more in our white paper on Rainwater Harvesting: Click here
The Broadway Office building will store more than 100,000 gallons of rain and condensate for treatment and reuse, with city recycled water backup. The system will supply 100% of the toilet, urinal, landscape, and cooling tower water make-up demand, with an estimated total site domestic water offset of 4 million gallons per year as compared to code minimum.
Our Austin Team can help you maximize your rebate and save you money over the lifespan of your building by integrating any number of water savings initiatives. Our team can develop a comprehensive water model to demonstrate the impacts of various systems and help you determine the right path forward.
For more information, contact water expert Jon Robertson today.
We’re introducing the first episode of our new Data-Driven Design Series, where we discuss with various experts both in and outside Glumac on cutting edge concepts we are currently integrating on building design projects across the world.
Here, we talk with Glumac Energy Engineer Gordon Stewart about his work building interactive dashboards that help owners make more informed, cost-effective decisions regarding the overall performance of their building.
As the energy grid across the West Coast becomes more reliant on clean power sources, Washington, Oregon, and California are responding with legislation that will push new and existing buildings to improve their energy efficiencies and carbon emissions. Our Energy team is here to help you chart a path to compliance and carbon reduction.
Here is a brief review of several upcoming pieces of legislation that are likely to impact West Coast owners in 2021 and beyond.
Washington State Clean Buildings Act
Set to phase in between 2026 and 2028, the Act sets new EUI targets buildings must meet, based on size building type and location.
Deadlines begin phasing in June 2026, for commercial buildings larger than 220,000 square feet, followed by buildings larger than 90,001 square feet in June 2027, and buildings larger than 50,000 square feet in June 2028.
While deadlines are several years out, the time to start paying attention to the Washington State Clean Buildings Act is now. There are multiple paths to compliance, however, and there are significant rebates available for early compliance.
Our energy group is assisting clients with early compliance to receive the maximum rebate possible. Learn more here. Or, contact Brian Goldcrump, our Northern Region Energy Lead, directly to discuss preparing your facility for compliance.
The 100 Percent Clean Energy Act of 2018
California’s 100 Percent Clean Energy Act is paving the way for cities across the state to craft their own electrification and decarbonization programs.
Also known as Senate Bill 100, the California Bill sets state-wide goal of powering all retail electricity sold in California with renewable and zero-carbon resources – e.g. solar, wind and others that do not emit greenhouse gases. Additionally, the bill:
- Updates the state’s Renewables Portfolio Standard to ensure that by 2030 at least 60 percent of California’s electricity is renewable (energy.ca.gov)
- Requires the Energy Commission, Public Utilities Commission and Air Resources Board to use programs under existing laws to achieve 100 percent clean electricity and issue a joint policy report on SB 100 by 2021 and every four years thereafter. (energy.ca.gov)
We are already working with several organizations looking to electrify and decarbonize. However, some in California are moving ahead of this timeline with commitments to be carbon neutral earlier than what is required by Senate Bill 100. We are partnering with the California State University system to chart a pathway toward carbon neutrality for all of its campuses by 2030. Many of these facilities require solutions beyond electrification to meet their accelerated timelines, and we already provided recommendations leading to 60% reduction in greenhouse gas emissions at the CSU Long Beach campus through a mix of onsite energy generation, HVAC retrofitting, carbon offset purchasing, and system electrification. Working closely with facilities staff and stakeholders at CSU, we’ve learned how to effectively develop tailored solutions to each client.
California Cities Push on with Building Electrification Requirements
So far, more than 40 cities across California have updated their building codes to reduce or eliminate their reliance on fossil fuels. This is being done largely through updates requiring new buildings be fully electrified. While no updates have been made to California’s Title 24 state energy code, these cities are forging ahead on their own to meet the state’s ambitious carbon reduction goals.
Using this interactive map you can see which municipalities have adopted some form of electrification. If you own or operate facilities in these areas that need updating for compliance, Brian Stern, our California Energy Team Lead can help. Click here to reach out.
We’re here to help you find clear solutions to complex problems. If you are in a jurisdiction with existing or upcoming electrification or decarbonization compliance mandates, we can help. To learn more about how we can help your facility meet its decarbonization goals, visit our energy team page.
As part of our work with Tetra Tech’s COVID-19 Task Force, we discussed with Dr. Willaim Bahnfleth, Chairman of the ASHRAE Epidemic Task Force, and Dr. Michael Kaiser, esteemed infectious disease expert, how personal environment style air purifiers can mitigate the spread of COVID-19 in the built environment, and create healthier spaces in the future.
Air filtration units are movable and offer a level of visual comfort to occupants. There are a variety of different personal environment systems capable of providing an enhanced level of safety and comfort in the built environment, including:
- HEPA filter units
- HEPA and carbon filter units
- HEPA and ultraviolet (UV) lighting units
- HEPA and titanium plate units
- HEPA, UV-C lighting, and bipolar ionization units
All of the above and combinations exist and are readily available in the marketplace. If the objective is infection control, our recommendation is the simplest units with a fan and HEPA filter only. These devices are efficient, cost-effective, and can capture 99.9 percent of the particles circulated. Strategically placed, these units can have a major impact on the health level of the individuals who occupy a space.
We’ve asked our expert about effectiveness and types of personal environments our clients should use. What follows is his response.
Is the reduction of particulates of a certain size in the air effective in mitigating spread?
Dr. William Bahnfleth: For SARS CoV-2, viral RNA has been found in very small particles that can easily be aerosolized. In some of his influenza research, Dr. Donald Milton, from the University of Maryland, found 90 percent of the viruses were in particles smaller than 5 microns in diameter. These devices can help remove particles that small, and they are very efficient. If you’re using HEPA filters with the highest penetrating particle size of 0.3 microns, that should be very effective against these aerosol droplet nuclei that are starting out mostly between 0.5 and 5 microns and reducing in size by 50 to 80 percent depending on the relative humidity.
Consider infection control in health care facilities. The basis of infection control in the most sensitive spaces is recirculation through HEPA filters. I don’t think that’s something that needs proof at this point. So, the question is mainly whether there is enough flow through the air cleaner and how well cleaned air is distributed. Even smoke testing just to see where the air is going will give you some idea of whether they’re being effective from a qualitative point of view in collecting the air that’s in the space.
Image courtesy of Hyundai Motors
Over the next several weeks, we will be publishing a series on Sustainable Building Design Challenges and how our Sustainability Consulting Team responds to them. We asked the group a series of questions related to building design. This is the first entry in that series.
How do we make sure today’s big picture thinking results in future individual occupant satisfaction?
Sustainable building design often requires big picture thinking, a focus on site, informed bio-climatic design, and scenario planning for buildings and their connected and supporting systems. However, without an early focus on health or user engagement, big picture thinking can miss the mark on how satisfied occupants are within the spaces and spaces they engage.
From our experience on the One Beverly Hills master plan, we found that visioning exercises benefit from balancing bio-climatic metrics that inform high performance design (e.g., daylight, solar heat gain, wind patterns, air and water quality) with their impacts to human health, equity and inclusion. Imagining user “day in the life” scenarios is helpful, as is the benefit of occupant surveys, public health research, climate change data for resiliency, and biophilic design.
Glumac’s Sustainability Team collaborated with Terrapin Bright Green on a biophilic design plan for California’s New Natural Resources HQ in Sacramento, and we successfully procured two LEED Pilot Innovation credits for our approach. Interventions included locally procured rammed earth blocks for the podium exterior, additional outdoor terraces to provide views, and connections to nature for a high percentage of desk spaces.
This project is part of a larger Urban District among State office buildings Glumac is playing an integral role in designing. Along with the Clifford L. Allenby Building and a new annex building to the State Capitol, the three buildings will share a singular central utility plant as well as a focus on electrified systems throughout each building to lower their operational carbon. The project team for the annex building is considering going fully electric by connecting to the central plant for cooling and providing heating at the building via heat exchangers and electric boilers. This type of district-level design requires big picture thinking at the start of the project, and when implemented, still allows for optimal occupant satisfaction on an individual level.
To learn more about of Government Office experience, head over to our project portfolio.
Workplace modifications due to COVID-19 are now also equally important. Glumac has already performed several Building Readiness Assessments for clients, which help provide achievable pathways toward updating or replacing systems to help mitigate viral spread within a new or existing space.
We begin by identifying the “most valuable spaces” for staff based on owner’s requirements and guidelines– for both interior and exterior spaces. It’s a goal-focused and metric-based approach utilizing data such as distance to greenspace; drinking water sources; shelter from wind and rain; heat islands; percentage of desks near sufficient daylight and distance to places of collaboration; and conversely, places for respite. These metrics as Key Performance Indicators (KPIs) can be quantified in BIM, overlaying the qualities that support these “most valuable spaces” with known high-performance strategies (e.g., east-west orientation, efficient skin-to-floor-plate ratio, opportunities for passive temperature control) and evaluate scenarios for performance against these KPIs. We then document these performance measures and strategies in the basis of design document, which guides the design toward healthy outcomes for occupants.
Let’s Design Something Great Together.
The Glumac Sustainability Team’s consulting approach is foremost to be an owner advocate: to carefully listen to an owner’s goals, then tailor a management process to fit, and finally lead its execution with a collaborative spirit and the talents of the design and construction team. We want to empower all design consultants to bring their best ideas forward for a project, and our role is to be sustainability advocates, to provide strong leadership in goal-setting, establish metrics, document progress, conduct research, bring innovative ideas forward, and ultimately, to celebrate our collective efforts with certification results.
Bipolar Ionization has been claimed to potentially mitigate, or reduce, the spread of bacteria and viruses throughout a space. Bipolar Ionization works by introducing positive and negative ions into the air. The ionization causes production of clusters of hydroxyl (OH) radicals, which are formed on the surface of microbes, removing hydrogen from the microbes’ cell walls, thereby inactivating potentially infectious particles. If not properly specified and installed, it may cause negative health effects.
To better understand this technology, we reviewed the most frequently asked questions with our COVID-19 Task Force; which includes Dr. William Bahnfleth, Dr. Michael Kaiser and engineers from Tetra Tech’s High Performance Buildings Group. Dr. Bahnfleth of Penn State University is the Chair of the ASHRAE COVID Taskforce. Dr. Kaiser has spent the majority of his career at the intersection of infectious disease and public health.
###
Do you have any experience with in-space installations (wall-mounted, etc.) or portable units that rely on passive diffusion of produced ions? Akin to a portable air filtering purifier?
DR. BAHNFLETH: There are/have been many portable ion generators. Most are consumer products of questionable quality control and performance. There may be better offerings from manufacturers who also do air handling unit installations.
Click here to read more.