Even when optimized, landscape irrigation is a significant source of water use within an urban community. However, water usage and costs can escalate when systems and equipment are broken or not controlled properly.
Here are a few common waste water culprits we find time and again during site-walks. Addressing them with a commissioning team can help realign your facility to achieve the kind of water efficiency that nets real savings:
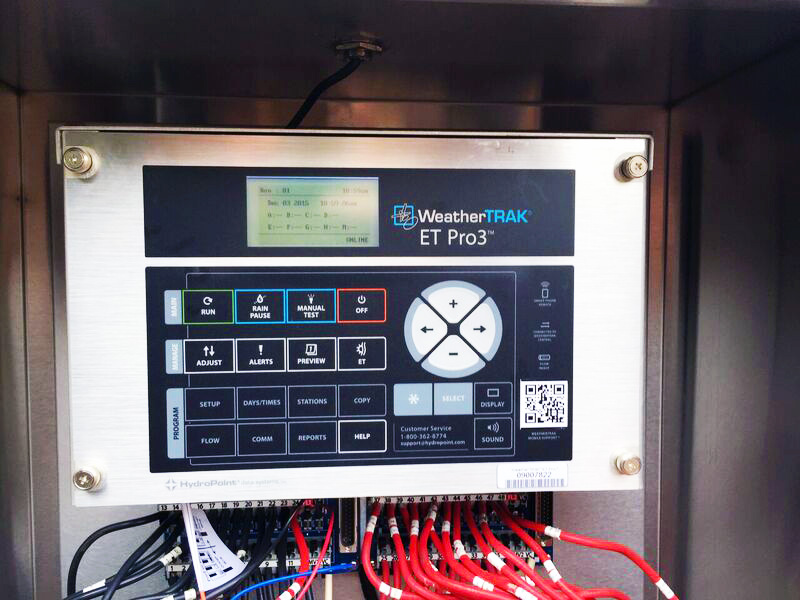
Controls
Problem – Ideally, irrigation controllers are programmed to allow just the right amount of water at the just the right interval for your landscape. But wasted water can easily occur when these controllers are outdated, not installed properly, or not optimized for your plant type, soil type, property slope, temperature, humidity, or exposure. Modern controllers aren’t perfect either. While they’re capable of receiving local weather data and decrease water output when it is cool or humid outside, often times they’re found to not be set up or programmed properly.
Solution – As they say, when something can go wrong, most likely it will go wrong. Controller setup should be verified and all functions tested to help achieve the usage savings those modern systems can provide. There can be hundreds of programmable values per site, which are necessary to provide the correct amount of water. A commissioning agent can help align those systems and set your facility up to start hitting some great water conservation benchmarks.
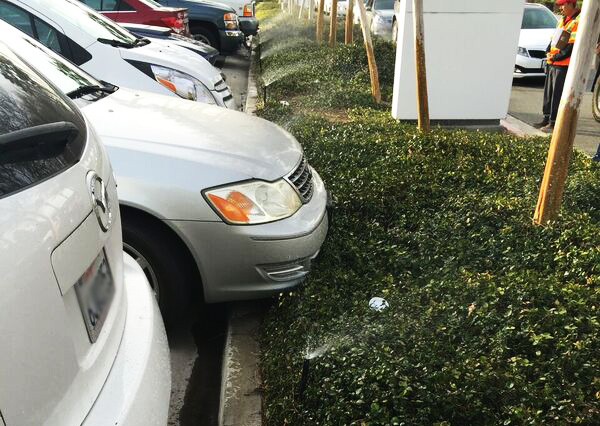
Poor Water Metering
Problem – It’s common to discover several significant system leaks when auditing a facility. System breaks are often the result of tree roots or accidental damage by workers. Main breaks also happen, and can be sudden and devastating. For instance, if a main line breaks and is losing 50 gallons per minute, a staggering total of 72,000 gallons of water would be lost in a 24-hour period. And on a different scale, if there are four locations with small, ½-gallon-per-minute leaks, it could add up to more than 1,000,000 gallons of water lost annually.
Solution – It is recommended that metering be in place not only to track general consumption, but to alert the system and user of leaks. Modern controllers can connect with meters and master valves to detect when there is a main line break or even when a sprinkler head has ruptured, and alert the user and shut down flow. Always be prepared – commissioning tests verify that parameters are set up correctly and can actually simulate breaks to confirm functionality.
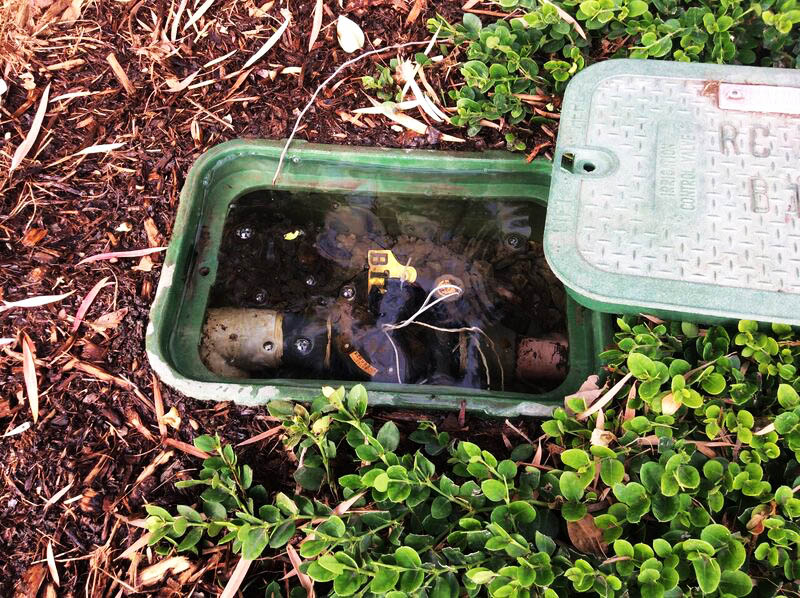
Degraded Systems
Problem – Over time, leaks develop at pipes, fittings, sprinkler caps, and seals. It’s inevitable. Common wear and tear, or simple system aging can cause things to break down, even at the most well maintained facility. And while simple degradation is expected, the resulting losses can be huge, often in the range of several gallons per minute, per zone, causing pooling, runoff, and major safety issues.
Solution – While a good landscape maintenance contractor will help identify some issues, it is necessary to perform routine system audits, repairs, and verification of completed work. Third party verification is key to ensuring all repairs – regardless of size or difficulty – have been completed properly.
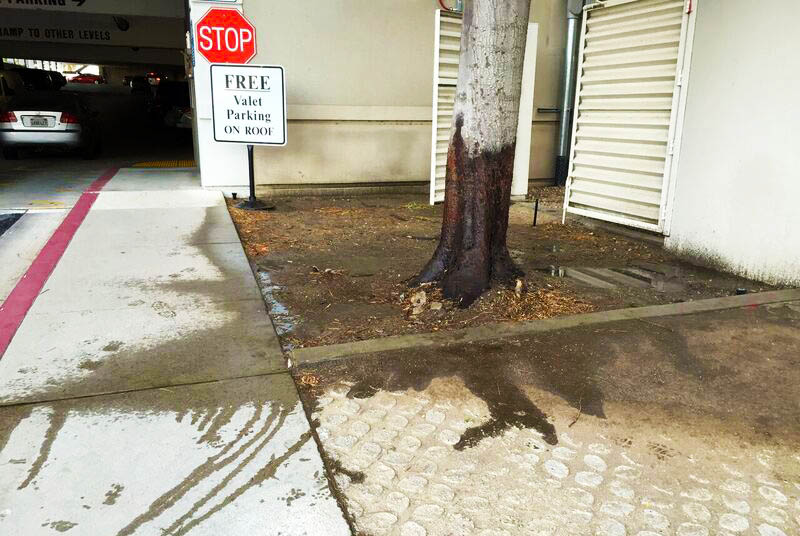
Inefficient Distribution
Problem – Distribution issues generally arise from poor application, replacements using the incorrect heads, changes to landscape, or improper system adjustments. Overspray and runoff are a common side effect of these problems, and compound system inefficiency.
Solution – Most facilities we audit have many heads that can be capped or reduced significantly. Pooling, overspray, and resulting runoff are commonly addressed by replacing heads with drip irrigation, variable arc nozzles, or simply adjusting flow. For example, we often see areas that have sprinklers where there are no longer plants. This leaves the possibility of capping (abandoning) these heads and redirecting flow to more needed areas. The commissioning process assists with identifying these issues and verifying corrections and adjustments.
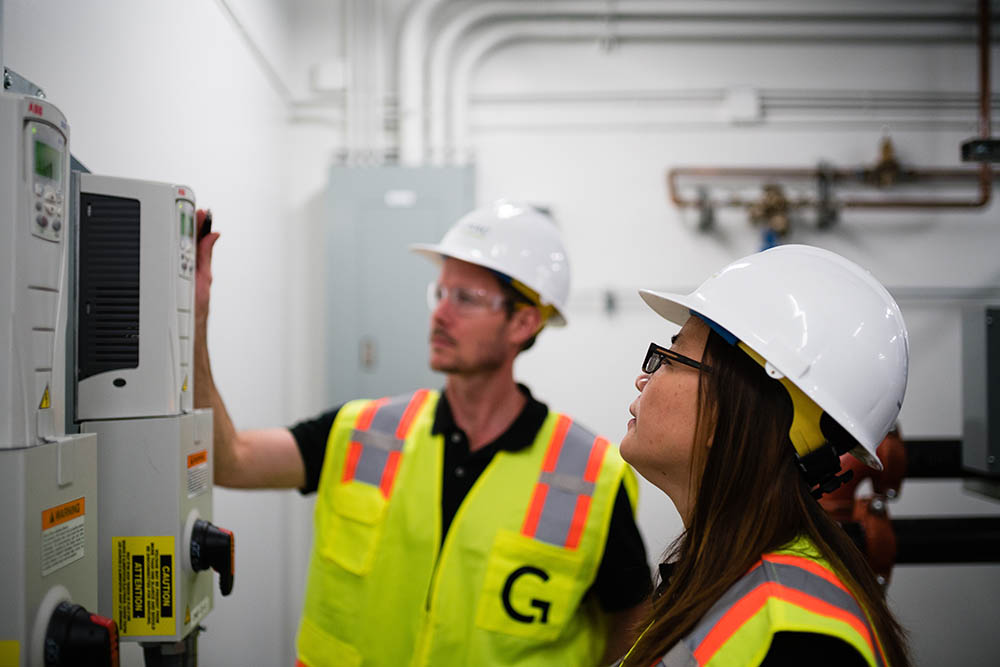
Operations & Maintenance
Problem – At sites with hundreds or even thousands of heads, it is difficult for a maintenance contractor to find all issues during routine visits. When you’re dealing with that sort of large-scale campus, it can be a tall order, even for the best. Often these visits concentrate more on landscaping and far less on surveying irrigation components. However the result is substantial water waste, public appearance concerns, and safety hazards.
Solution – In cooperation with facilities and/or the landscape contractor, a commissioning team can partner on a routine survey and evaluation report. This will assist in identifying outstanding waste issues and cost-effective solutions. An annual survey may be sufficient for sites less than five years old, bi-annually for sites 5-10 years old, and a quarterly survey might be appropriate for those older than 10 years. Where smart controllers are installed, a monthly report can be generated to include alarms of potential problems, and operations and maintenance staff can be trained on how to properly respond to these reports.
The complexity of landscape irrigation systems should not be underestimated. When it comes to maintenance requirements and reoccurring issues, systems left untended will wash potential savings out with the wasted water they’re designed to conserve. Commissioning teams are here to help you recoup the savings you’re expecting from the optimized systems you’ve invested in. An initial system audit and repair can be followed by a program of regular maintenance, surveys, and reporting as part of your sustainable building program.
To learn more about Glumac’s commissioning services, please email Aaron Schneider at [email protected].
Water is becoming a precious resource, particularly in the Western United States, where many of our clients live and work.
In 2016, we are invigorating our focus on water conservation in the built environment, and further establishing ourselves as industry leaders in this area. With El Niño forecasting rain to drought-stricken states, we see this as a time to draw attention to the presence of water and to underscore the need to conserve what little water we now have.
Together as leaders in sustainability for the built environment, we can be part of the solution. Through efficient systems and quality design, we can help create a sustainable future.
See our 2016 New Year’s video message and email us at [email protected] to learn more about water and energy saving measures for your projects.
By now, we all know that low access to daylight can be detrimental to our health. Eye strain, exhaustion, and weakening mental health are all issues that share a root cause in poor access to light.
But what if the implications of access to daylight went beyond wellness and energy savings, and we could prove it was inextricably linked to increases in productivity? If we were able to tell hour-by-hour (even minute-by-minute) how optimized a person’s mind and body is under specific lighting conditions, we would be able to leverage that information toward creating a workplace that goes beyond simply housing business activity, and actually improves the quality of work being done.
In fact, we already can. It’s called Circadian Lighting: a lighting system designed to tap into the proven cycles our bodies’ follow each day, based on the position, angle, and color of natural sunlight at any given time. These cycles are known to lighting designers and medical researchers as “circadian rhythms,” and a circadian lighting system is tailored specifically to maximize our functionality.
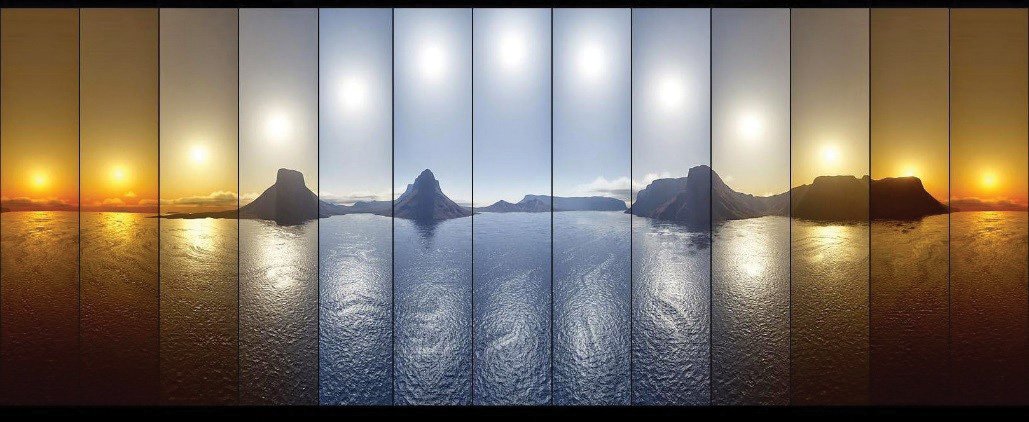
For example, in a traditional office space we tend to either have electric lighting we can turn on or off, but there is rarely a distinction in the color of that light, or its brightness (think: rows of fluorescents hung uniformly below a white dropped ceiling… your eyes may be hurting already). This works against occupants’ naturally occurring circadian rhythms and can cause dramatic decreases in overall wellness and productivity. What lighting designers seek to do with a circadian lighting system is mimic the behavior of the sun and incorporate it into the everyday work environment to benefit occupants by creating a comfortable environment and actually increasing productivity. This can be achieved with a few methods that we’ll explore in this article, including introducing natural light into areas through architectural elements and by mimicking the solar sequence through tunable LED lighting.
“Recent studies of office worker performance show that those with the best views of natural light perform better on tests of mental function and memory recall.”
When we examine the pattern of the sun through its 24-hour cycle, we notice that the light it emits more complex than light and dark. The color and intensity of sunlight changes throughout the day: Warm amber light at sunrise slowly changes into a cooler, brighter light during the day, before warming back into an amber light at sunset. Human vision follows this cycle throughout the day. The eye consists of cells that act as photoreceptors, called rods and cones, which play a vital role. Cones sense changes in color and bright light, while rods sense changes in low light levels. The eye sends these signals to the brain to trigger the release of serotonin (the body’s natural antidepressant) during the day and melatonin (a hormone effecting sleep) at night. This is what creates our circadian rhythm and promotes our mental and physical health, our mood, and our energy.
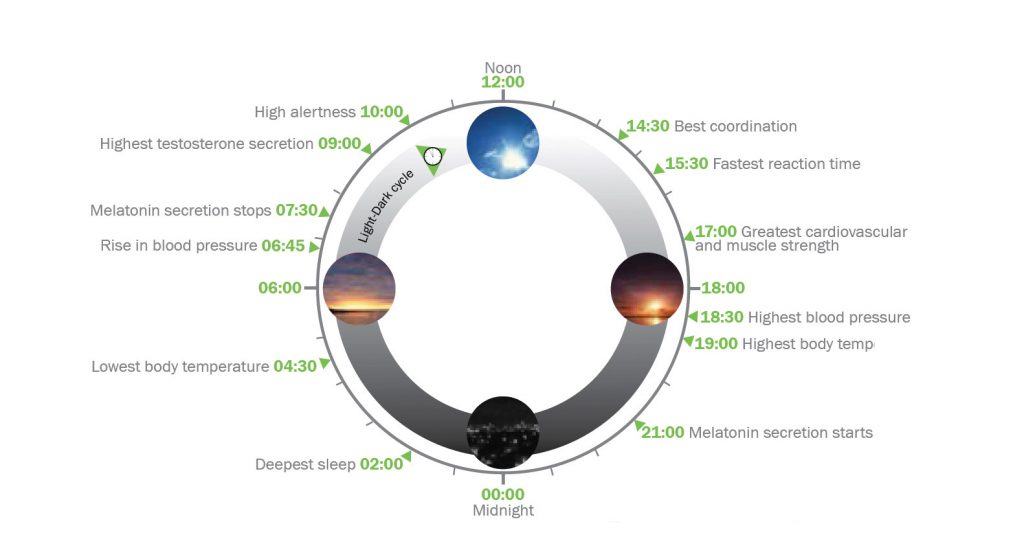
The Benefits of Circadian Lighting
As noted earlier, lighting designers are able to leverage data on how the average human body reacts to create a lighting system that understands what kind of light an occupant needs to perform at optimum levels on an hour-to-hour (or as we see in the image above, a minute-to-minute) basis. Just like with a healthy diet, if we feed the body what it needs, it will perform better.
The benefits of human-centric circadian lighting design include:
- Increased alertness in the morning
- Productivity and concentration improvements
- Improved mood
- Reduced hyperactivity
- Reduction in errors and accidents
- Faster cognitive processing
- Improved sleep
Recent studies of office worker performance have shown that those with the best possible view of natural light performed between 10% and 25%1 better on tests of mental function and memory recall. On the other hand, those with poor views or no view at all (think high cubical partitions, heavy glare, basement offices etc.), reported increases in fatigue and decreases in overall speed of performance. These variables can be controlled with circadian lighting design. Incorporating daylighting in the architecture can boost not just the performance of a building, but of those who occupy it as well.
Circadian lighting has shown to have useful applications in the healthcare industry as well, benefiting patients and institutions alike by actually decreasing average length of patient stays. A recent study published in Building and Environment reported findings that patients with direct access to morning light were seeing their stays shortened by anywhere from 16% to 41%2.
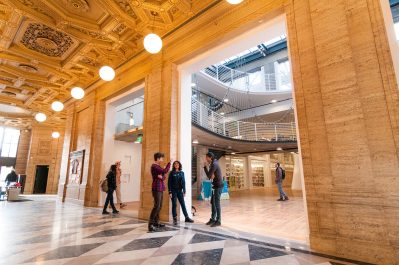
How it’s done
Existing technologies now allow us to recreate the sun’s daily path to help directly manage occupants’ circadian rhythms, particular in spaces that have poor access to natural light. LED light fixtures can mimic the solar color shift with color changing technology and DALI color changing controls, creating the same health benefits we see from natural daylight. For LED circadian lighting to work, a controls system must be used that is setup to handle the job, and at this point in time, that is the biggest cost. Numerous manufactures have their own system designed already and it can be done using a variety of products. From imitation skylights like Arbor Light and Coelux, to downlights like those made available by Ketra, the base models already exist. A full cycle of human-centric lighting has already become a reality for workplaces and healthcare facilities across the United States, and they are seeing the productivity benefits in real time.
That being said, natural light has the most direct effect on our circadian rhythms. And harnessing it for our interior spaces is the most effective way to optimize its effects. However, this means more than just allowing light into a space. Giant windows can often overheat those nearby in afternoon sun, do little to deflect glare, and leave much of the space totally unaffected. Proper daylighting involves controlling light and getting as much effective illuminance to target areas as possible, while minimizing heat gain and glare. Architectural design elements like light shelves and louvers can bring more light into the interior of a building when added to glazing. They can also direct the light deeper into a space. Exterior overhangs and vertical fins on the glazing walls of a building can mitigate glare and heat gain.
At GLUMAC, we believe circadian lighting is the future of lighting design. To learn more about our work, email our Lighting Studio at [email protected].
Click here to read the full Circadian Lighting Green Paper.
References
1. [Heschong, Lisa. Heschong Mahone Group. “Windows and Offices: A Study of Office Worker Performance and the Indoor Environment.” California Energy Commission: Pacific Gas and Electric Company. Fair Oaks, California. 2003a.]↩
2. [Choi, Joon-Ho. “Impacts of Indoor Daylight Environments on Patient Average Length of Stay (ALOS) in a Healthcare Facility.” Building and Environment 50 (2012): 65-75. Web]↩
ASHRAE is nearing the final stages of publishing its own energy modeling standard.
Energy efficiency and sustainability are playing an increasing role in design decisions. As such, defining a minimum standard of care for energy simulation is becoming crucial. The ASHRAE standard – open for public comment until May 9, 2016 – is the result of four years of internal discussions and considerations from a committee made up of energy analysts, energy software developers, researchers and government entities from across North America – including Glumac’s Ross Farris, P.E. With the goal of creating a standard for integrating energy modeling into the design process for high performance buildings, the goal is to provide a consistent approach for building energy modeling across the industry.
“The hope is that this standard will provide a framework that identifies a minimum level of energy analysis for new construction and major renovation projects. The ultimate goal is to aid the design process and enable design team members to make informed decisions,” Farris says. “It’s not a document that dictates how to create an energy model, but rather how to provide benefit to the design process through energy modeling. We believe this new ASHRAE standard will benefit cities, counties, states, building rating systems, and other agencies that might adopt the standard as a requirement within their programs for building design and construction. Our committee has worked diligently over the last four years to create this document, and we look forward to now being able to obtain comments from the public for incorporation into the standard.”
The standard is designed to apply to all new buildings or major renovations of existing buildings that use energy modeling in the design process. Once approved, this could drive greater levels of sustainability in the built environment. Requirements highlighted in the new standard include: at least two cycles of energy modeling during the design process, one being completed in the early stages of design when the energy impacts of design decisions can greatly impact energy use and HVAC system sizing. Modeling cycles have been defined to bring benefit at all stages of the design process. Additionally, owners would be required to integrate energy performance goals directly into their project requirements.
The standard is intended to get a project team thinking about the energy impacts of their design from the beginning of the design process in order to make informed decisions which will ideally create a more energy-efficient building design.
This is an inclusive process, and we encourage all who read this to take a look at the standard and provide comments.
If you have further questions about this process or energy modeling in general, please contact Ross Farris at [email protected].
For Earth Day 2016, Glumac Sacramento’s Green Team decided to do something that would have both an immediate and lasting impact on our office, employees, and the Earth. So we decided to plant a garden filled with some of our favorite fruits, vegetables, and herbs. To get started, staff donated what they could to keep the garden thriving, and in the end we all get to share the fruits (and veggies) of our labor!
Here is a brief synopsis of how we did it, none of which would have been possible without the hard work and good will of our staff!
Plan your garden.
If you’re going to create a shared garden, the best advice we can give is to take advantage of the shared experience of your team. Thankfully, Glumac Sacramento was not short on experience, nor on people willing to lend a hand. We decided to dedicate two weekends, one to get the planter boxes ready and another to plant. Planting only took up one Sunday morning, so all up this was a 3-day endeavor.
Get the materials.
Fortunately we had pretty much all of the tools we needed, including a rototiller, wheel barrows, saws, etc. We had soil delivered by truck (to cut down on cost and packaging materials), as well as decomposed granite for the walkways. Being organic was of the utmost importance, so we also set up a compost area, which we will use to fertilize the garden. We used redwood for the planter boxes, and built them ourselves. This was not only a cost-saver, but also allowed us to customize them to the exact size we needed. There was already a spigot in place at the site of the garden, so we bought the materials required to make our own drip system, fully equipped with a timer (there is a slight benefit to having an office full of engineers…). Finally, we picked up some wire fencing to help defend against curious critters—you’ll find no pesticides in our garden!
Build the garden.
Rally the troops! Building a garden from scratch is no easy feat, especially if the ground is as dry and rocky as ours here in Northern California. The ground we were working with only seemed hospitable to weeds, so we had to start by using a rototiller and removing what seemed like 18,000,000 rocks (probably more like 500). These rocks eventually made their way back to the garden, acting as a liner along the bottom of the beds to keep in the soil. Once the ground was cleared, we placed, leveled, and lined the beds. Soil was then added and packed down as much as possible. Believe it or not, everything up to this point was done in just ONE DAY!
Finish prepping the beds.
We let the beds sit overnight and returned the next morning rejuvenated! We added the remaining soil to the beds, packing it in as much as possible, and put what was left outside the beds for melons and other unruly vegetation. Simultaneously, the drip system was being assembled and installed. The drip system was tested, pizza was consumed, and everyone went home after a successful second day.
Plant.
Now, the fun part! To get everyone involved, we asked employees to donate plants and seeds. In doing so, we hoped to create a sense of ownership and ensure that we are only planting what we will actually use. Planting took the better part of Sunday morning, but it was more than worth it. Now, we get to watch as our garden grows and thrives for years to come!
When we first started in the A/E/C industry, it was exciting to be a part of the amazing and innovative work involved in creating sustainable buildings. However, from as far back as middle school, being one of a small handful of females in STEM-related courses was the norm. And today, a point of ongoing discussion with our colleagues is how few women pursue education in engineering, and how even fewer pursue construction and MEP design. We began examining why, and what we as a firm, and an industry at large, could do to change that.
We all knew the statistics: that right now, just 20 of the chief executives in the Fortune 500 are women, but that organizations with the highest representation of women in leadership positions demonstrate better financial performance – a 35% higher return on equity and a 34% higher total return to stakeholders.[1] In short, it’s good for business. But the question remains: what is keeping young women from pursuing a career in this or any other STEM-related industry despite the encouraging growth forecasts? What is it about the established tradition of the industry that is preventing women from believing it is something they would be good at and enjoy?
Projections for the next decade are promising for the commercial real estate and construction industries. Opportunities for STEM-related jobs are expected to grow by 17% by 2024, compared to other industries, which project at around 12%.[2] When this is coupled with a significantly more narrow pay gap (on average women in the construction industry earn 93.4% of a man’s base salary, compared to just 82.1%[3] throughout the United States), the pitch to young women is a simple one: the STEM industry offers potential for a career that is as lucrative as it is challenging and stimulating. And if we can encourage entry into this industry now, at the dawn of this period of accelerated growth, these young women will be more prepared 10 years from now to take their place at the table and step confidently into leadership roles.
“Changing how young girls are educated about these subjects, along with increasing the visibility of women in these industries, these statistics will begin to even out.”
Despite all this, even now in conversations with our female engineers, we still learn they were only one of two or three women in their graduating class. Perceptions of this being a male-oriented field begin at a very young age. However, great progress is being made in laying the ground work for a future passion for math and science at an early age. By changing how young girls are educated about these subjects, along with increasing the visibility of women in these industries, these statistics will begin to even out.
It’s possible the answer lies in the different ways men and women perceive their value in the workplace. A now well-known anecdote from Facebook COO Sheryl Sandberg’s bestseller Lean In cites an internal study conducted by Hewlett-Packard that found the majority of its male employees would apply for a job despite only meeting 60% of the qualifications. Women, however, were likely to apply only after being sure they met at least 90%. She also cites a story from the mother of former Harvard president Larry Summers, who, upon being hired as an economist by the Standard Oil Company, was told by her boss, “I am so glad to have you. I figure I am getting the same brains for less money.” Back then, she took this as a compliment. That was the 1940s, but more than 60 years later many women in the workplace still battle this misaligned perception of the skills they offer and their true value in the marketplace.
“When I first started college in 2008, my program boasted one of the highest percentages of women in the School of Engineering at about 50%. But by graduation, that had reduced to 12%,” says Staci Ashcraft, Mechanical Designer. “I remember so many instances of blatant sexism; professors telling female students they should drop out to be housewives, or that the only women who belonged in engineering were the tom-boys. There was no encouraging voice to say that we didn’t have to eventually make the choice between being a wife and mother or having a successful career.”
As an MEP consulting firm, we decided that recognizing this value goes beyond the abstract idea of being open to simply hiring more women engineers. It means taking steps toward creating an office that better supports the everyday needs of professional women. Implementing amenities and benefits into offices and HR plans geared toward women not only make a company attractive to top young female recruits, but demonstrates that they are valued. Mother’s rooms and nursing equipment – which we integrated into our offices and provided respectively – robust maternity leave, flex time for new mothers, daycare all begin to address the challenges that are simple realities of working mothers. Being a new parent is a stressful time, and making an effort at decreasing that stress in the workplace can go a long way in building a lasting relationship with an employee.
“Resources like mentorship, professional development and advocacy also go a long way in establishing for women the same level of support and normalcy men have traditionally enjoyed.”
Nicole Isle, BADT, LEED AP BD+C, Chief Sustainability Strategist shared, “When I returned to work after maturity leave, I felt truly supported. My colleagues were accommodating and collaborative in helping me manage my new work-life priorities. The wellness room in our office was also a huge benefit to me. It was comfortable and private. I could take care of my own needs as well as manage emails with my laptop or smart phone. I think it starts with a level of comfort in the office to engage in conversation about personal topics. When you’re able to do that, you can work in partnership with your employer.”
Resources like mentorship, professional development and advocacy also go a long way in establishing for women the same level of support and normalcy men have traditionally enjoyed. They also go a long way in combating “rite of passage” issues so many young professional women report dealing with—coworkers who’ve struggled with workplace issues in the past insisting younger staff personally overcome the same challenges. And encouraging involvement in STEM and ACE mentorship/educational programs foster a community of young leaders. Armed with this understanding, we go beyond the numbers of pay equality and growth to demonstrate what a truly equitable workplace looks like, and see the social and economic benefits that lie within.
“Having a mentor is so important in developing professionally,” says Christine Culver, PE, Lighting Designer, “When I was first starting out as an engineer, it wasn’t easy to see how to get to the next level. I always have a formal mentorship with regular scheduled meetings as well as a few people within my company, outside my company and even outside my industry that I consider casual mentors. It’s important to always ask questions, get advice, and search for new ideas.”
We’re also seeing the number of women in Glumac’s associates group grow, and encouraging them to pursue educational opportunities throughout our offices. These are steps we’ve made in the right direction. But there are many more to take. And at a future stakeholders’ meeting, the next generation of female STEM superstars will be well represented. This industry is primed for growth. It’s where jobs and demand are. And if we’re not providing these opportunities, we’re not creating a sustainable and vibrant industry.
For more information on how you can get involved with ACE or STEM-related programs, contact Angela Sheehan and Angela Templin at [email protected].
Water conservation has become one of today’s most urgent challenges to sustainable design.Â
As the world becomes more aware and engaged in sustainability at a lifestyle and cultural level, the social and economic benefits of investing in water conservation are becoming more globally apparent and compelling. Solutions like low-flow plumbing fixtures can decrease a facility’s water bill, and an artificial wetland can ease burdens on city sewage systems and minimize potable water use. But there’s a missed conversation here. Greywater reuse and potable water preservation dominate these discussions, and while those solutions certainly carry merit, one important aspect of conservation is often neglected: process water.
That is, the water used in a building’s mechanical systems to heat, cool and otherwise support and maintain reliable operation. But just like the human body, buildings need clean water to function properly and efficiently. The challenge is that, because of its limited re-usability, process water is a major culprit for water use and waste in large buildings and industrial facilities. As it is passed through a system over and again, process water acquires corrosive elements—such as metals or salts—that taint it to a point where it is no longer pure enough for use. The resulting water, known as “blow down water,” has a high level of total dissolved solids (TDS), and can damage the system—creating major energy inefficiencies, increased need for water and, eventually, the need for expensive infrastructure replacements.
There is no one-size-fits-all solution. The trick is… addressing the issues on site rather than
pushing them down stream.
To successfully expand our water conservation efforts, we must begin incorporating ways to lessen the amount of water necessary for a building’s basic operation. There are several innovative approaches currently in use to help get the most out of the water we have already. Condensate recovery and rainwater catchment can reduce how heavily a system leans on potable water. In turn, water that is no longer usable for these processes can, once properly conditioned, be reused to flush toilets before being passed through another filtration and used again for drip irrigation. These solutions increase the lifespan and usability of water already existing in a system, and help further divorce a building from local water sources, conserving what’s available to the community.
Process Water Environmental Factors
A litany of variable environmental factors, based on building type, region and climate, also present unique challenges for process water conservation and reuse. For example, in many commercial buildings, this water is typically used to reject heat in the cooling tower or air handling unit. But this comes at a cost of lost water through evaporation and drift—water that is simply blown away by the wind and lost. These are waste scenarios that are preventable with infrastructure adjustments. However, finding ways on site to maintain or extend the re-usability of blow down water, which is in many cases dumped into the waste water drain, is critical to achieving greater levels of conservation.
The number of times water can be recycled through a system remains a great barrier toward conservation. However, increasing the number of process water reuse cycles can make a real impact. In California, for example, code requires that water be recycled a minimum of four times before it is discharged as blow down. With thoughtful design, we can easily achieve eight cycles, and truly innovative systems can achieve up to 20, depending on several environmental factors. If, for example, an average mixed-use development uses 60,000,000 gallons of water per year, and 25% of that alone go to heating. That’s 15,000,000 gallons per year. If we are able to increase the number of cycles the system can handle, this becomes an area where we can greatly reduce consumption.
Finding Solutions Before a Problem Arises
There is no one-size-fits-all solution. The trick to determining the best approach is finding that sweet spot between a building’s need and water reuse cycles, and addressing the issues on site rather than pushing them down stream. The percentages of process water vary greatly between industrial, healthcare and commercial buildings. In the coming months, we will address the process water issues of each of these facility types, to create a more concrete understanding of just how large of a challenge to water conservation this truly is.
For more information, please contact Neil Steiner.
With 2014 revenues at $38 billion and more than 130,000 employees company-wide, Oracle has plans. Big plans. These included reaching their internal IT growth targets for 2014 with a forward-looking plan to support IT growth needs for the next several years. Accordingly, Oracle moved forward with the build-out of the UCF Phase 2 Data Center space in West Jordan, Utah. The Glumac-lead design team master planned the UCF Phase 2 space to provide for 30,000 sf of highly reliable and highly available Tier III space. The UCF Phase 2 master plan included building the 30,000 sf of data center space in six modular 5,000 sf builds.
Headquartered in Redwood Shores, California, Oracle is an American multi-national computer technology corporation most known for its comprehensive and fully integrated stack of cloud applications, platform services and engineered systems. Perhaps less known, but equally impressive, is its commitment to sustainability practices that are embedded in every aspect of its business operations, making Oracle a sustainability leader in the high-tech industry.
With more than two decades of experience implementing sustainable energy, water and waste management practices, Oracle has set some high sustainability goals for themselves. By 2016, Oracle targets a 10% reduction in energy use per employee and 6% improvement in Power Usage Effectiveness (PUE) in production data centers. The Oracle Utah Compute Facility Cell 2.1 in West Jordan, Utah, is one part of this pursuit.
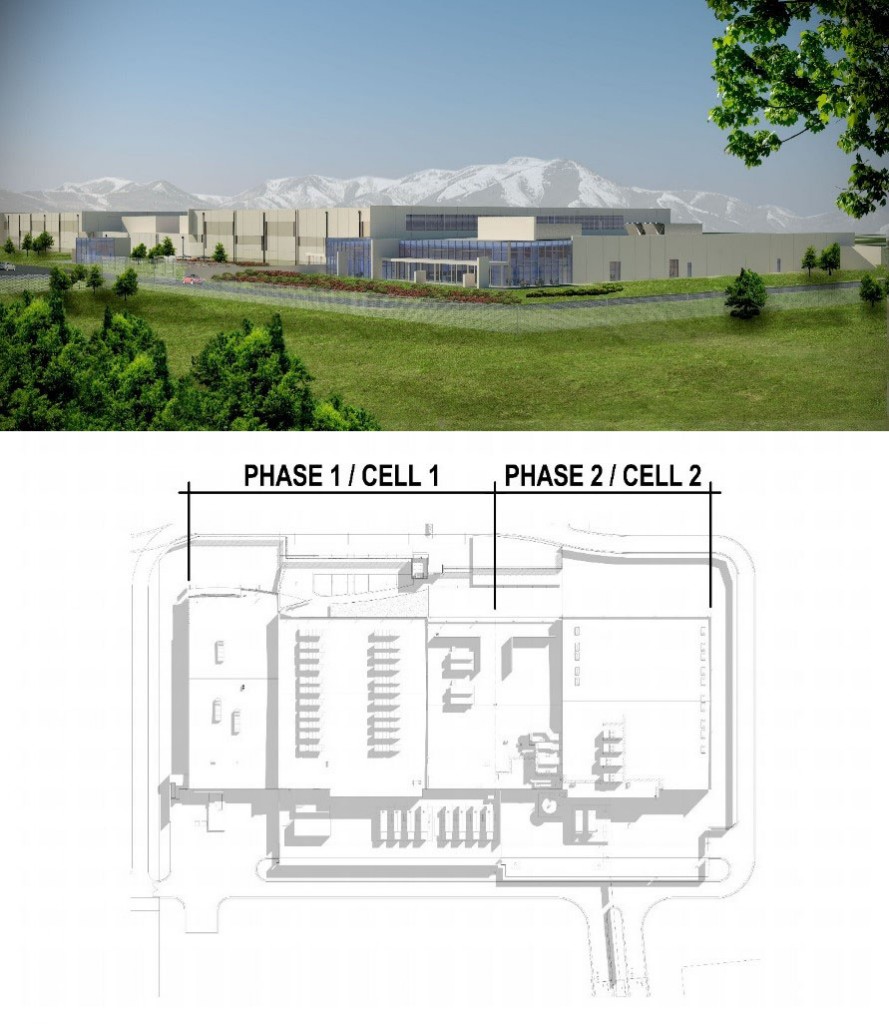
UCF Phase 2 was originally planned as a 1,100-rack data center with the entire space populated in a single build. Oracle modified their Phase 2 plans to incorporate a phased build approach that provides for six 5,500 sf rack “Cells” to fit within the existing UCF Phase 2 shell space. Modular data center designs enable a “pay as you grow” path forward. Modular builds also allow for clients to more effectively meet their evolving IT user requirements with the newest technology improvements as well as allowing the owner to take advantage of the newest technologies available to the supporting MEP designs.
This Design-Collaboration approach used on the UCF Phase 2 project heavily emphasized open collaboration between Oracle, the Glumac-led design team and the Holder Construction-led construction team. Early face-to-face strategy sessions led to a strong Basis of Design and established open project communications, a strong sense of partnering and the critical project goals. Weekly project collaboration calls and monthly on-site meetings kept the project on track.
The project’s Design-Collaboration approach was highly successful. Some of the key Oracle project metrics like optimized project cost, low PUE, ease of installation and maintenance were successfully addressed through the Design-Collaboration approach. The open project leadership created a safe, constructive environment that encouraged free flow of ideas leading to the most optimized project cost, low total cost of ownership (TCO), and industry leading energy efficiency. The owner, design, and construction teams coordinated solutions through an always current Revit BIM Model.
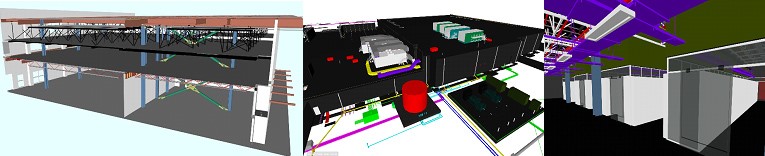
The results were clear. The Oracle UCF Cell 2.1 Phase 2 project was completed on time, meeting the user’s requirements and costs were on budget. The PUE of the space was calculated to be 1.22, which is a 24% reduction as compared with Utah industry averages of 1.60.
 Critical IT Load |
 PUE |  Yearly kWhr Utilized |
 Notes | |
 Oracle UCF, Phase 1 | 5.8 MW |  1.29 |  ~65,500,000 |
UCF Phase 1 was designed for 7.2 MW. Critical load and PUE
represented measured values as of 1/1/15
|
 Oracle UCF, Phase 2 Cell 2.1 |  1.2 MW |  1.22 |  ~10,850,000 |  Calculated PUE |
 Utah Energy Code |  1.2 MW |  1.6 |  ~15,500,000 |  Calculated PUE |
Further, the low PUE will help Oracle’s original sustainability goals of achieving 6% reduction in data center PUE and will save $250k/year compared to a similar facility built to Utah energy code standards.
The Oracle Utah Compute Facility Cell 2.1 demonstrates that data centers can be both sustainable and reliable. Taking a Design-Collaboration approach to modular pay-as-you-go growth and practicing consistent, open communication and collaboration brought the project to completion very successfully. Ultimately, the key element of project success started from the top. It was Oracle’s commitment to sustainability that set the bar for the project. In making these goals a priority, Oracle selected an expert design and construction team that shared the same vision.
To learn more about similar mission critical and sustainability-related projects, please email us at [email protected].
Glumac’s Christine Culver, an electrical engineer and lighting designer based in our Sacramento office, spoke and served as a guest mentor at a Nontraditional Employment for Women (NEW) program at Sierra College. The event connected young girls with mentors from various industries to encourage the pursuit of nontraditional education and careers that lead to high-wage and in-demand jobs.
TO LEARN MORE ABOUT NEW, CLICK HERE
Mission College in Santa Clara, California, is getting a new front door.
Soon, the first building you will see when approaching the campus will be the new Phase II Main Building Replacement. Set to complete in the fall of 2017, the 100,000-square-foot, three-story building incorporates multiple programs including Student Services, Counseling, as well as academic classrooms and college administrative and faculty offices. The facility will serve 1,000 students and faculty, and serve as the new main entry point for the campus.
Initially, this new build may appear similar to any other successful higher educational facility designed to meet impressive energy-efficiency standards. Originally targeting LEED Gold certification, the project is now striving for LEED Platinum. How it achieved that, however, is a story of value-oriented collaboration and strong alignment of intentions between Mission College students, faculty and management; the design team of architects at Lionakis; and the MEP systems engineers at Glumac.
That collaboration resulted in the implementation of several sustainable systems by Glumac’s MEP team, including displacement and natural ventilation, indirect and direct evaporative cooling (IDEC), radiant floor for comfortable and stable heating and cooling, solar thermal power for generating hot water, daylighting and LED lighting with extensive controls that enable responsive spaces to occupant needs, and a water loop that utilizes greywater for the HVAC and non-potable plumbing systems – a new approach for the college as the campus had previously only used greywater for irrigation purposes.
Lean + Collaborative Approach to Design
Drawing from their success in the healthcare field, Lionakis proposed a Lean approach for the Phase II Main Building Replacement project. Lean is a business methodology that examines process flow, scheduling and waste mitigation issues. The goal is to achieve operational excellence. A means to do this is to “choose by advantage,” wherein the project team collaboratively identifies only the advantages of different solutions for the end-user of a space and/or building system. Effectively, it is a process that “pushes to the positive” instead of “pulling from the negative.” The team viewed each choice through the prism of highest value to Mission College and their end users of the facility. Through analyzing all decisions from a value-return perspective, the project provided the greatest value return to Mission College while conforming to its overall budget and exceeding its initial sustainability goals. One major example of this was cutting potable water usage by 75% and the costs of potable water in half.
A key part of the design collaboration also included a series of charettes between students, faculty, Lionakis and Glumac. Students wanted a comfortable environment with minimal glare, optimal thermal comfort and learning environments that were enhanced by good acoustical design. Glumac’s engineers designed mechanical, electrical, plumbing and lighting systems through an integrated design process that provided the most appropriate systems for this project including the previously noted MEP systems.
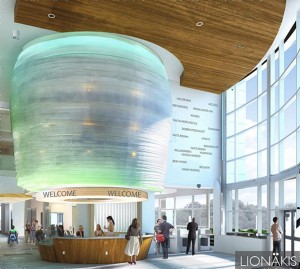
LEED Commitment
Drawing from their success in the healthcare field, Lionakis proposed a Lean approach for LEED Commitment Mission College’s commitment to sustainability requires that all new buildings achieve a minimum level of LEED Silver certification, campus-wide composting and recycling efforts, the use of eco-friendly cleaning products and classes that focus on habitat enhancement and sustainable aquaponics. So, it comes as no surprise that students and faculty alike wanted to create buildings that provide a sustainable legacy for future students, faculty and administrators.
The design team understood these goals and responded with a design that targeted a strong level of LEED Gold certification. However, after analyzing the energy resource inputs and potential energy adjustments within the project’s budgetary reach, the design team revised their target to strive for LEED Platinum certification. The project is now under construction with Gilbane functioning as Construction Manager and the LEED Coordinator on the construction side of the project.

Energy-Use Database for Planning Accuracy
The design team used Glumac’s Building Energy Consumption Survey (GBECS) to tune the energy efficiency of the Main Building. GBECS is a tracking and feedback tool that monitors energy and water performance. This data adds to and compares existing data in Glumac’s portfolio database. This energy-use database produces accurate energy models that ultimately provide reliable information both owners and architects can use to inform their investment and planning decisions. For Mission College, GBECS helped the design team maximize its efficiency goals, minimize maintenance, and exceed its LEED objectives.
Ultimately, the project addressed systems at the utility and district scale helping create a pathway to LEED Platinum that worked within Mission College’s project budget. The Lean and collaborative approach, along with Glumac’s energy usage database, fostered the creativity needed to achieve the end-user savings and functionality necessary to position Mission College as a sustainable campus.
To learn more about similar higher educational and sustainability-related projects, please email us at [email protected].
DESIGN & CONSTRUCTION TEAM
Owner: West Valley Community College District: Mission College Campus
Architect: Lionakis
MEP/Energy/Lighting Design Engineers: Glumac
Construction Manager: Gilbane
Civil Engineer: Sandis
Acoustics/IT: SFMI
The Oregon Convention Center’s commitment to sustainability has been evident since construction on the facility was first completed in 1990. Operated by Metro, the Portland area regional governance organization, the Oregon Convention Center was conceived and constructed to serve as a beacon of sustainability in the Pacific Northwest.
For the last 25 years, the Oregon Convention Center’s staff has worked tirelessly toward its stated mission to be the greenest events facility in the world, and the first choice for domestic and international green meetings. In November of 2004, it became the first convention center in the world to achieve LEED-EBOM certification from the U.S. Green Building Council, and in the years since has reached LEED Platinum. Considering it is a facility that operates 24 hours a day and houses nearly a million square feet of functional event space, the achievement is remarkable. In fact, it is one of only a small number of convention centers in the world to reach LEED Platinum.
Its efforts to certify and re-certify for LEED designations have resulted in major environmental and community benefits, thanks largely to some herculean waste diversion efforts. Nearly 70 percent of waste produced by the facility has been diverted away from landfills. Nearly 30,000 pounds of food has been donated to the Oregon Food Bank. And some 66,000 pounds of food has been donated to other Portland area shelters.
To prepare for its upcoming recertification in 2014, the Oregon Convention Center hired Glumac’s commissioning team in the summer of 2010 to undergo a retro-commissioning process to help improve its energy and atmosphere systems in order to earn LEED Gold. But once the team arrived, it determined there was enough low-cost and no-cost solutions to leap frog that designation and reach the rarified air of LEED Platinum. The scorecard for the Energy and Atmosphere certification has the most requirements of any category required to certify for LEED Platinum, and the Oregon Convention Center currently meets more than of any of other LEED Platinum convention center.
“We hired Glumac to help analyze the more difficult or hard-to-find energy savings measures,” said Ryan Thorpe, former director of operations for the OCC.
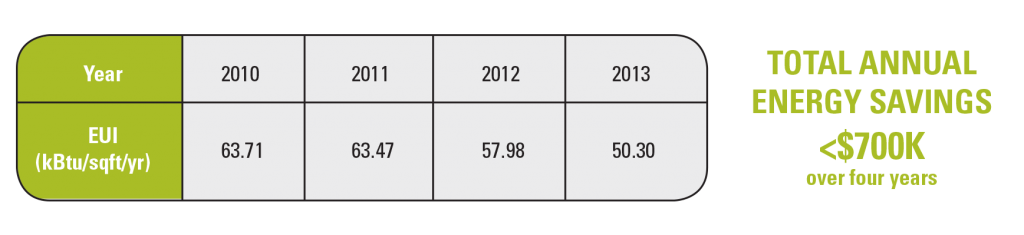
During the retro-commissioning process it was discovered that Oregon Convention Center’s boilers were running nonstop during the high heat of midsummer, causing the cooling system to work overtime, which in turn created comfort level issues throughout the venue. By recommending replacement of the existing non-condensing boilers and then shutting them down in the summer months, Glumac was able to help the Oregon Convention Center see a dramatic drop in energy outputs and costs, particularly between June and September. In addition, the pressure settings for the chilled water pumps were too high, much of the time operating at as much as 90%, creating a lot of excess energy usage. By reducing chilled water system differential pressure set point and modifying its staging control sequences, major energy efficiency improvements were achieved.
Also during the retro-commissioning process, the Glumac team discovered that heavy accumulation of dust and dirt in the variable air volume (VAV) terminal units had caused them to fall out of calibration. This resulted in difficulties maintaining accurate comfort level readings, which caused wasted energy. With the help of the Glumac team, the Oregon Convention Center maintenance staff installed filters designed to prevent excess particles from reaching the sensors. Vast improvements in the functionality VAV units were gained once they were rebalanced.
Great teamwork between Glumac, various contractors including a testing and balancing firm and a controls team, and the Oregon Convention Center’s facilities staff have made the convention center a sustainable building that works. The Oregon Convention Center’s investment in retro-commissioning and its effort to reach LEED Platinum have resulted a tremendous EUI reduction, and in a total annual energy savings amounting to more than $700,000 over four years since 2010. With improved operational efficiency, improvements in staff productivity have resulted in increased occupant satisfaction and decreased labor costs, contributing to measurable improvements in the surrounding community, making the Oregon Convention Center a green building that truly works.
To learn more about Glumac’s Commissioning services or how energy conservation measures can save you money, contact me, Kevin Dow at [email protected].
The Coachella Valley has long been home to a cluster of oases in the rocky desert of Southern California. One of these sought out destinations is the Indian Wells Tennis Garden. Opened in 2000, the facility, nestled into the Old Hollywood getaway of Indian Wells, has undergone an award-winning renovation – recently having been recognized by the United States Tennis Association as its 2014 Facility of the Year. In addition to designing the mechanical, electrical, plumbing and technology integration systems, Glumac designed the lighting for the interiors and exteriors of the multi-court, multi-stadium facility, combining a modern, efficient lighting system with the existing, retro fixtures that line the exteriors.
“Typically stadium lighting is somewhat predictable. There are a couple of showcase opportunities, but it’s more or less just trying to get people around,” Lighting Designer Brian Hahnlen said. “The fun parts were the landscape lighting, the circulation lighting around the campus and the sports lighting. So we wanted to show a little pizzazz.”
As the host of the BNP Paribas Open, one of the largest tennis events in the world, the Indian Wells Tennis Garden offers plenty of opportunity to show off. With the goal of preserving that Old Hollywood feel while blending in more modern lighting techniques, the lighting team looked to the venue’s natural elements for inspiration.
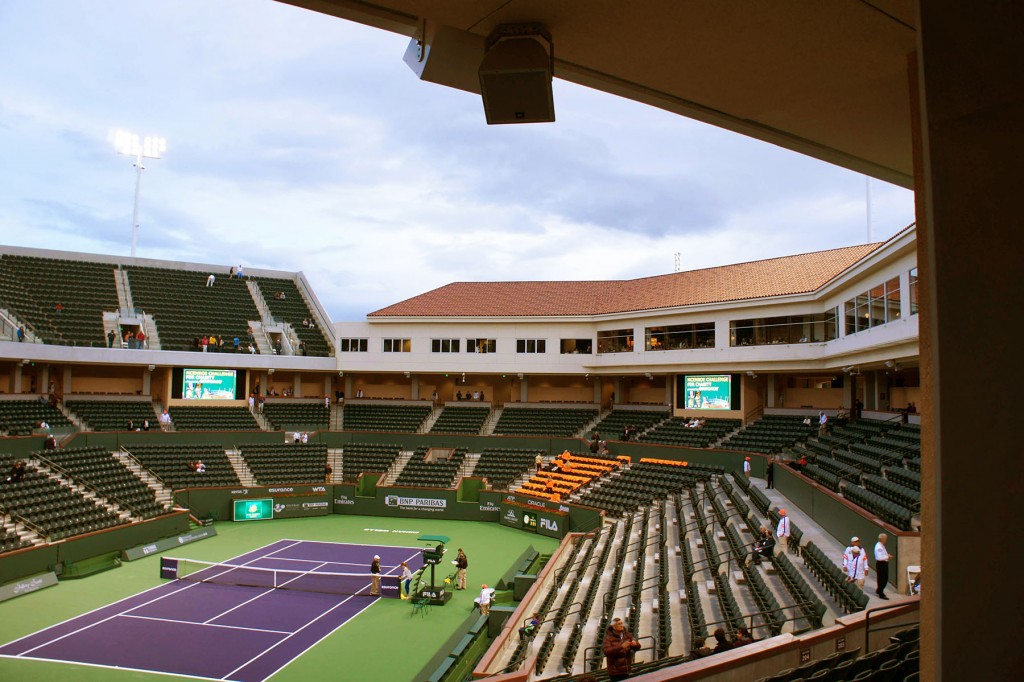
“There are palm trees everywhere, and we used them as a type of light source,” Hahnlen said. “We up-lit some of them to give you the feel that it’s brighter than it actually is, and from the same location we down-lit the pedestrian pathways. It was a huge improvement.”
Glumac’s lighting team was challenged with not just improving the ambiance of the outdoor venue, but also providing lighting to satisfy the needs of a top-tier sporting event for both audience members and television broadcasts. The ESPN standard for lighting was a major requirement that gave the team a difficult set of constraints with regards to Glumac’s sustainability agenda. When dealing with high-definition broadcasting, the lighting needs to be bright and uniform, which means efficiency can easily be pushed into the back seat.
“The ESPN standard really drives the output level,” Hahnlen said. “The owners of the stadium really wanted at least 100 footcandles horizontal. The ESPN standard starts out with the vertical footcandles and the horizontal kind of blends in to it. So, in getting the ESPN criteria, we ended up with somewhere between 150 and 180 footcandles. Now that sounds absolutely ridiculous from a sustainability stand point, but for HD cameras, you really need that much.”
We made up for the day-to-day use in the controls.
For the sports lighting, we have step-down control so they don’t have to run the lighting systems
non-stop at full blast.
Having to meet standards with such heavy usage requirements required some innovative thinking on the part of the Glumac team. They designed variable controls that not only allow the facility to present their events in a variety of ways, but also tamp down usage during certain low-traffic days to conserve energy.
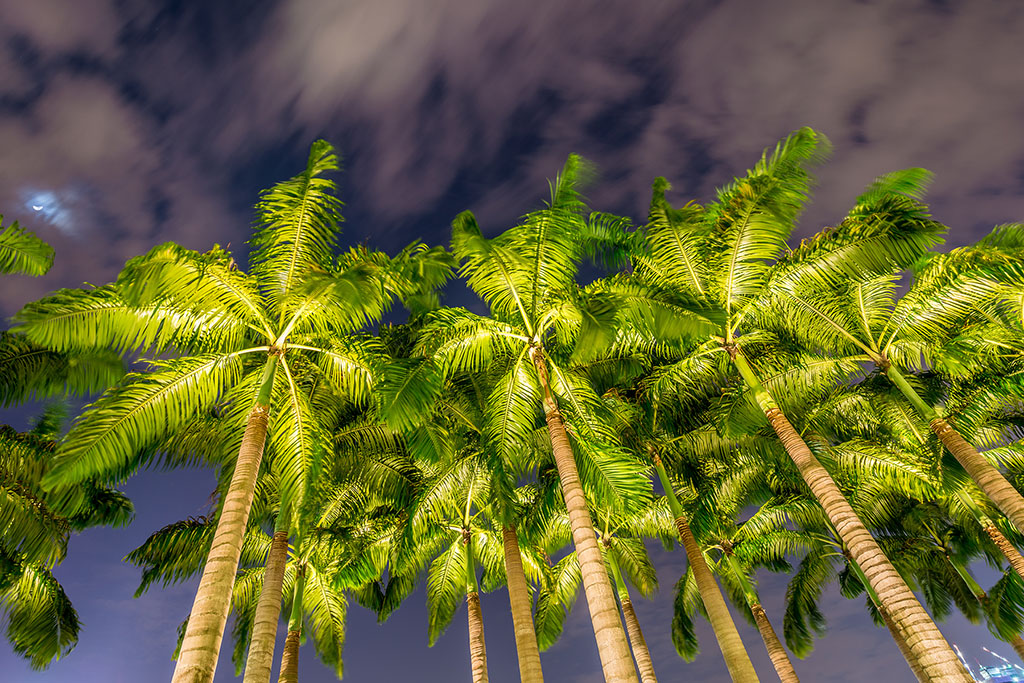
“It’s zoned and circuited so they can use the light as they need,” Hahnlen said. “So we made up for the day-to-day use in the controls. For the sports lighting, we have step-down control so they don’t have to run the lighting systems non-stop at full blast. For the landscape lighting, the controls were tuned to leave the ambient up-lighting off and the down-lighting at 50 percent when they don’t need it. All of those things are layered into the control system, saving energy that would have otherwise been wasted in a comparable facility.”
Finding inroads to sustainable practices for a facility that requires specific energy outputs was a challenge. But the Indian Wells Tennis Garden now features the tools to maintain energy efficiency, save money, while not sacrificing its well-known standard of excellence.
————————
For more information on lighting design for your project, please contact Jesse Smith, Senior Lighting Designer, Glumac Lighting Studio, via [email protected]
Clad in a new envelope of glass and steel with a sloping rooftop solar parasol, the Edith Green-Wendell Wyatt (EGWW) building bears little resemblance to the white concrete façade of the original 1970s building. Exterior shading and radiant systems provide excellent comfort and energy efficiency. But energy-optimized buildings can’t be handed over “as is” at completion and be expected to thrive. A year of post-occupancy commissioning proved key in transforming this federal building from an energy hog to a high performance workplace.
Energy savings goals for the building were specified by the project’s funding source, the 2009 American Recovery and Reinvestment Act (ARRA). The federal stimulus funding required energy savings of 30% over ASHRAE/IESNA Standard 90.1- 2007, and a 55% reduction in fossil fuel energy over a 2003 Commercial Buildings Energy Consumption Survey (CBECS) baseline. The building team pursued an integrated design approach, which began with a building skin optimized for energy efficiency via innovative envelope shading devices, optimized window-to-wall ratios, and excellent daylighting.
Hydronic radiant panels meet the remaining heating and cooling loads, supported by a dedicated outdoor air system. To reduce potable water use, the team implemented rainwater reuse by adapting an existing, unused basement shooting range into a 165,000 gallon rainwater storage tank.
On the roof, 13,000 ft2 of photovoltaic panels create a distinct signature on the skyline. The dramatic transformation of the building’s exterior appearance has captured the attention of passersby and created a landmark in downtown Portland.
With the U.S. General Services Administration (GSA) as a driver, the project team fostered a cooperative process that resulted in cost savings, quality improvements, and optimum ongoing building performance. Innovative commissioning and energy modeling helped enhance system design, installation, and eventually operation.
Click here to read the full article at High Performance Buildings Magazine.
The University of Washington Bothell campus had two important needs. As a burgeoning destination for students in the Snohomish and King counties of WA, UW had to increase its enrollment capacity. They also needed to meet the academic demands of its students, local community, and regional industry, specifically in the field of science, technology, engineering and math (STEM).
The new Discovery Hall was the answer to both, now serving an additional 1,000 students and housing the UW Bothell School of STEM. With sleek style, impressive sustainability features, and flexible space programming, the new 74,000 sf building opened for classes in fall 2014. The facility includes general meeting spaces, offices, lecture hall, classrooms, and laboratories for chemistry, life science, physics, electrical engineering, software development and geographic information systems.
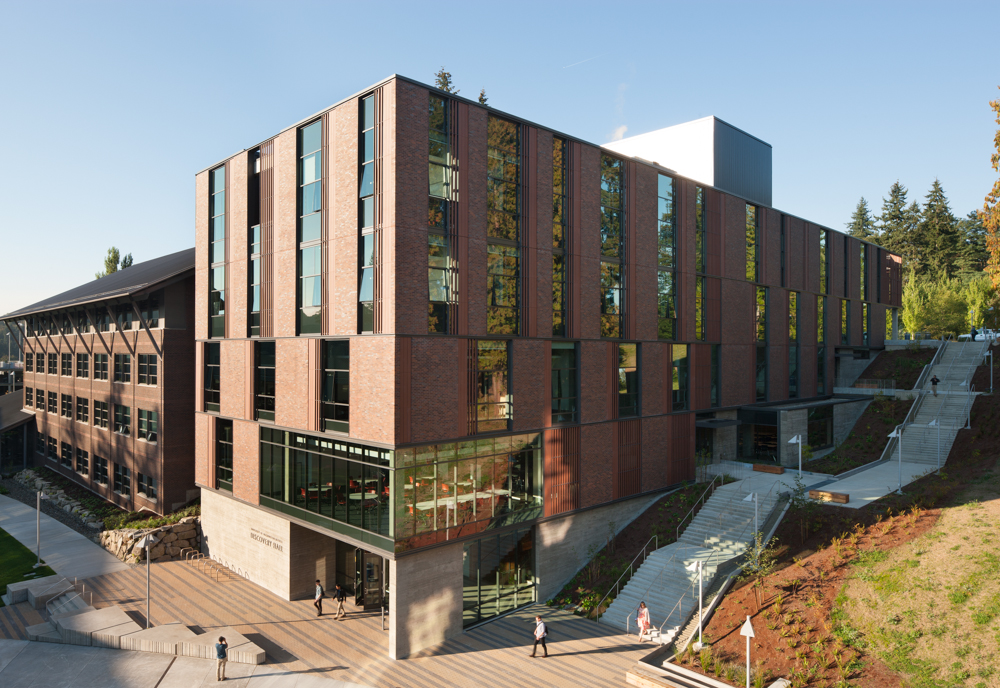
Environmental stewardship is the hallmark of UW Bothell. As such, Discovery Hall demonstrates the best in an energy-efficient and ecologically thoughtful facility. The building design integrates many sustainability features. Operable windows, chilled beams, displacement ventilation, heat recovery and solar hot water reduce energy use. Efficient lighting, daylighting and lighting controls also minimize energy needs. Low-flow plumbing fixtures economize water needs and a stormwater catchment system filters and feeds water to the campus’ 58-acre wetlands. Last, the east-west orientation and high-performance glazing optimize solar control and reduce heating and cooling loads. As a result, anticipated energy use comes in 30% lower than a comparable facility and is targeting LEED Gold certification.
Discovery Hall represents a much-needed catalyst to support an estimated future 350 career-ready graduates per year and facilitate greater STEM programs. It is also an embodiment of UW Bothell’s commitment to sustainability and an encouraging legacy for the future of higher education.
AWARDS:
2014 AIA Seattle Award of Merit
2014 AIA Portland Merit Award
DESIGN TEAM:
Owner: University of Washington
Architect: THA Architecture
Landscape architect: Walker Macy MC/CM
Mechanical/electrical engineer: Glumac
Structural engineer: PCS Structural Solutions
Civil engineer: OTAK
GC/CM (General Contractor/Construction Manager): Lease Crutcher Lewis
Lighting Designer: Biella Lighting
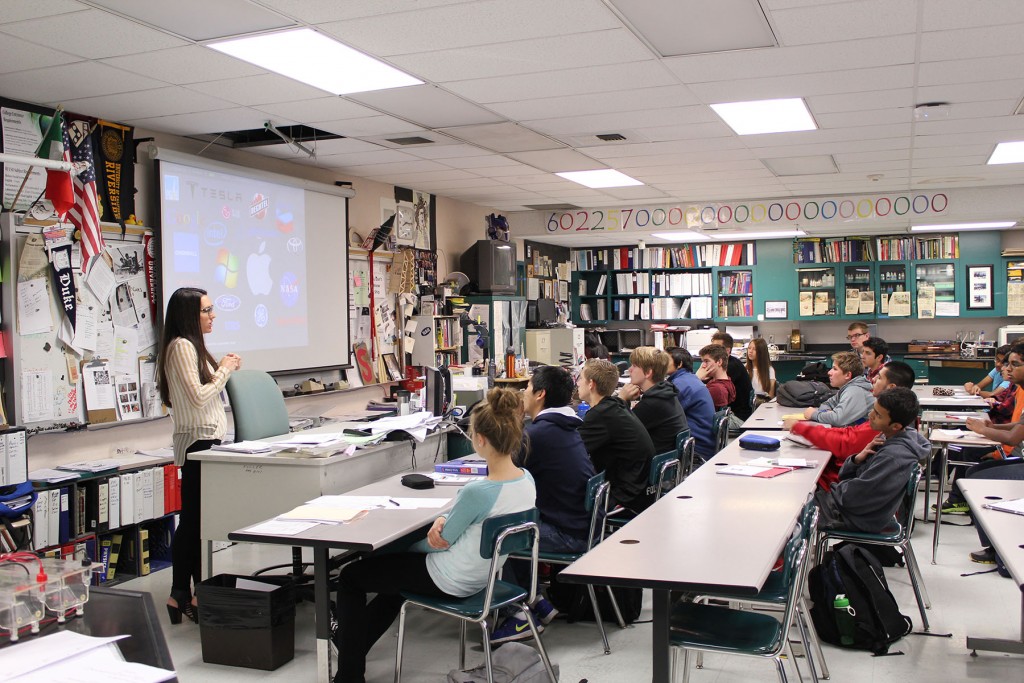
Glumac’s Christine Culver, EIT, LEED GA and LC, worked with Folsom High School’s Physics and Engineering classes to bring the engineering profession to life and talk about its career possibilities.  Culver’s visit was part of Glumac Sacramento’s local outreach to celebrate National Engineers Week (Feb. 22-28) and to inform and inspire kids with a passion and interest in the field.
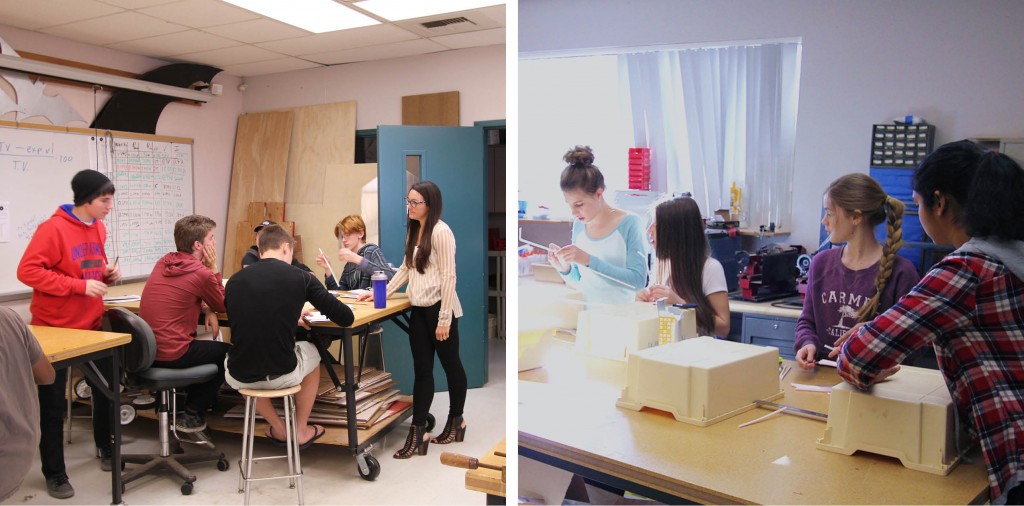
“Many students don’t realize how important engineering is to the products and services we use every day,” Culver explains. “From our smartphones to the cars we use, or the buildings we live and work in, everything is designed. The industry always needs fresh ideas and there are exciting career opportunities out there.”
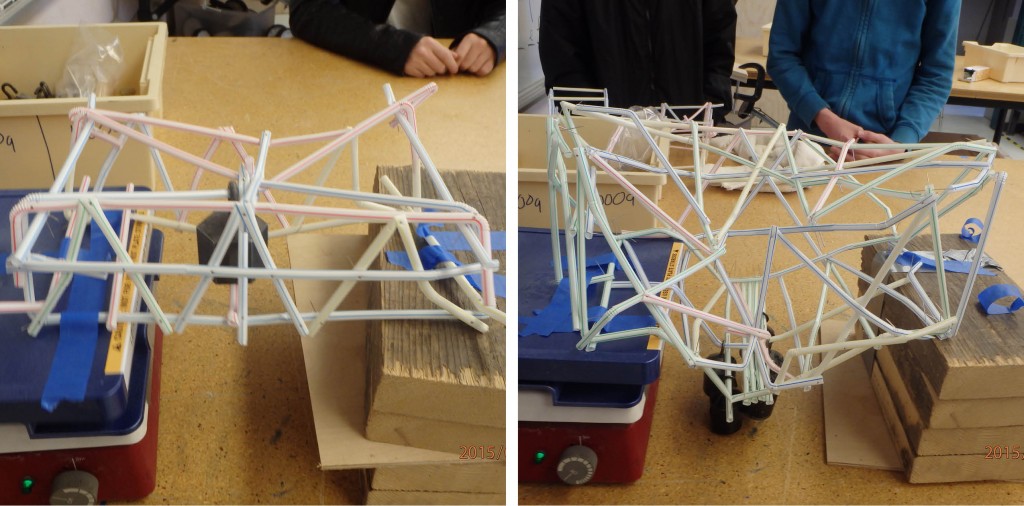
Students learned about the engineering process (brainstorm, design, build, test, redesign), the assortment of engineering fields, including companies and colleges known for their focus on engineering, as well as what we do at Glumac. Given her passion for lighting design, Culver also showed the students how different filtered lenses can bend and alter the same light source in different ways. They were then tasked to work in teams to build straw bridges that were practical, beautiful and functional. The bridges’ functionality was tested by the load it could handle and the torque it could withstand.
For some creative ideas on how you can make a difference to STEM students, click here. Or, to support your local ACE Mentor Program, click here.
We’d love to visit your school too! It you’d like a Glumac engineer speak to students in your area, let us know by email.
The decision to build the new 68,500-seat Levi’s ® Stadium, a venue owned by the Santa Clara Stadium Authority, was never about simply constructing a new home for its city’s beloved football team, the San Francisco 49ers. It was intended to be the first of its kind in sustainability: the first stadium in the United States to receive LEED Gold certification as new construction. In order for the stadium to obtain LEED Gold, the project had to pursue not only the prerequisite commissioning credit, but also the enhanced commissioning and Measurement & Verification credits. Glumac provided these services and helped achieve the goal of the most sustainable stadium to date.
Sustainability was a defining feature of this project, and was incorporated in to everything from the field to the roof. HNTB Architects designed the state-of-the-art stadium and a joint venture between Turner Construction and Devcon Construction (TDJV) built it. The stadium has several features that set it apart from other entertainment/sports venue, including electric vehicle charging stations, photovoltaic panels atop pedestrian bridges and suite tower, a first-in-the-league vegetative green roof, and an extensive dual-plumbed recycled water system design to serve the green roof, playing field, cooling towers, and all restroom toilet/urinal fixtures.
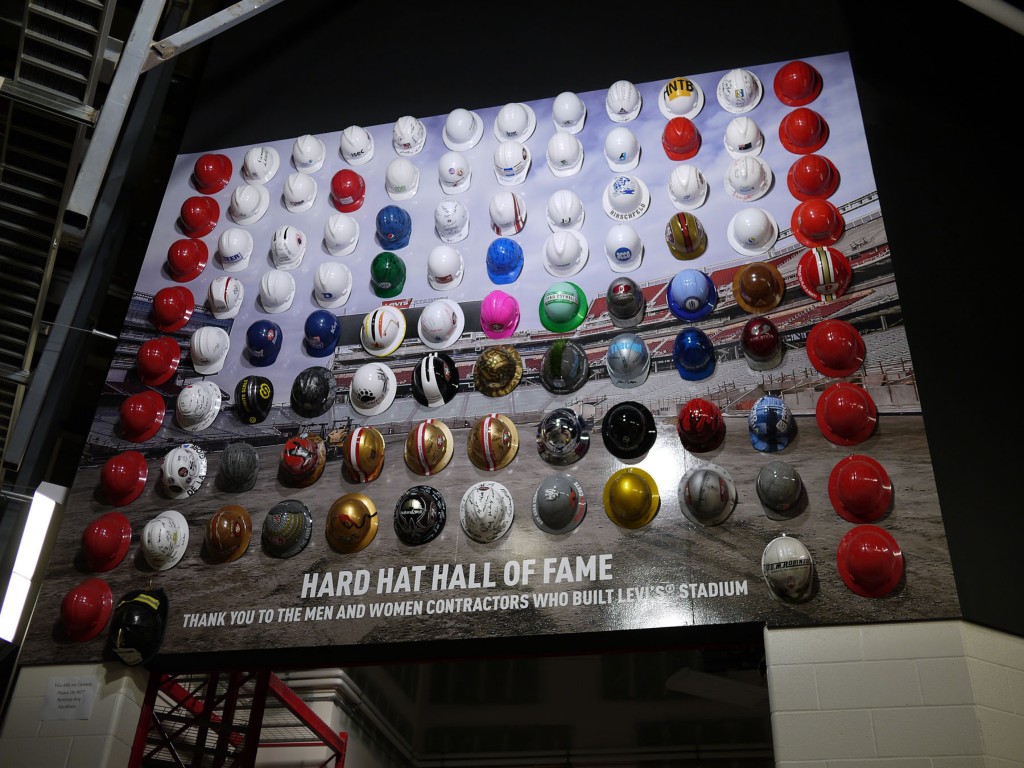
The enormity of this 1.85 million sqft project was striking. The project had 45 air handler units (AHU’s) and rooftop units with 12 unique sequences of operations resulting in the writing of 12 different functional acceptance tests. In addition to the AHU’s, there were 80 water-source heat pumps and more than 450 variable-air volume boxes. A hot water system, consisting of five 3,000 MBH boilers, serves the stadium, while a 2,450 ton central cooling tower plant provided the cooling. Additional commissioned equipment included more than 100 exhaust fans ranging from electrical & toilet exhaust fans to smoke and CO exhaust fans, a dehumidification unit for the hydrotherapy room, a triplex water softener skid and domestic/recycled water booster pumps.
With an aggressive construction schedule and stadium grand opening date fast approaching, Glumac worked efficiently with the general contractor, sub-contractors, and air and water balancers to outline a commissioning schedule that would allow certain areas to be commissioned and turned over earlier. To ensure coordination and quick resolution to commissioning-related issues, regular weekly meetings started a full year before project completion in order to facilitate the successful execution of the project. The stadium operations team participated early in the development, and was a key part of the commissioning process. They were active participants in the startup and commissioning of all equipment, participating in all commissioning meetings, and providing valuable input that ensured commissioning could continue to progress forward.
On July 21, 2014, Levi’s ® Stadium achieved its goal of LEED Gold certification. But, the stadium continues to go beyond. As part of the ongoing sustainability effort they have incorporated an interactive educational learning exhibit into a 20,000sqft 49ers Museum Presented by Sony for fans to experience. The 49ers Museum Presented by Sony also offers educational programs to teach students in local area schools the importance of sustainable practices. There is a commitment to maintain energy efficiency, promote sustainability, and be a “first-class celebration of the 49ers past, present and future.”
For further information on the commissioning for your next LEED project, please contact me at [email protected].
References
“Sustainability.” http://www.levisstadium.com/about/sustainability/ Accessed: Nov. 25, 2014.
“About the 49ers Museum.” http://www.levisstadium.com/museum/ Accessed: Nov. 25, 2014.
Nicole Isle, chief sustainability strategist with Glumac’s Portland office, believes more building designs should capitalize on the human attraction to nature.
Isle, who has a background in biology, is leading the engineering firm’s investigation into biophilic design. The emerging philosophy is based on the concept of biophilia, which means “love of life,” and seeks to find design solutions that enable people to enjoy this affinity to nature indoors.
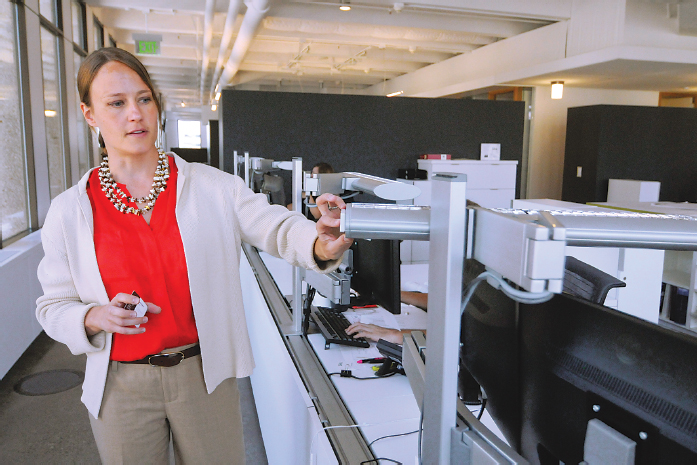
This can be as simple as letting in sunlight and fresh air, or using carpet or furniture patterns with naturalistic designs or fractals. Other biophilic design concepts include ventilation systems that periodically let out puffs of air to mimic the air fluctuations found outside, or indoor spaces tailored to fit primal needs.
“Biophilia is a reminder that nature
supports us in so many ways.”
Architectural designs inspired by nature not only are aesthetically pleasing, Isle said, but also make economic sense. Numerous studies have shown that connecting office workers to nature raises productivity levels by stimulating brain activity and keeping people alert, she said. Retailers have found that customers buy more of a product displayed in a portion of the store lit by skylights. Studies in schools and hospitals have shown access to daylight can help students learn and patients heal faster.
“There is economic value in connecting people to nature … so we started our own research into it,” Isle said.
A focus on our instinctual response to nature is how biophilia differs from the concept of biomimicry – using plant and animal behavior to solve human issues, she said.
“Biophilia is this innate connection to nature,” Isle said. “We need it like we need healthy food and exercise.”
Earlier this summer, Glumac hosted a lecture series, “Biophilia in the Built Environment,” in Seattle, San Francisco and Los Angeles; experts shared lessons with the design and build industry. Firm staffers have incorporated biophilic design into newer offices in Shanghai and Los Angeles, and are hoping to convince clients to include it in their projects, Isle said. Pointing out the economic benefits will be key to selling the importance of biophilic design, she said.
“This is the path that we’ve chosen because we find it very interesting,” she said. “There is a lot of good data. Now we can talk to our clients with real numbers. It helps build the business case for it. You’re also talking about improving the ability for your employees to perform, so there’s a real human element.”
Glumac staffers were inspired to learn more about biophilia via the work of Bill Browning, founder of New York City-based environmental consulting and strategic planning firm Terrapin Bright Green. Browning, who spoke at all three of the Glumac biophilia events, is one of the authors of a Terrapin Bright Green report titled “The Economics of Biophilia: Why Designing with Nature in Mind Makes Financial Sense.”
“There’s real science being done on why our connection to nature is so important.”
The report points out that scientific studies show employers can improve worker productivity and profits with simple office space improvements, such as providing access to plants, natural views and daylight. One such study found that workers in an administrative building at the University of Oregon, who had views of trees and landscape, were less likely to take sick days and spend more time at their desks than those with no view.
Scientific research that backs up the benefits of biophilic design is one reason why Jeff Roberts, a senior architectural designer at Portland-based SERA Architects, incorporates the concept into all the projects he works on.
“Biophilia is grounded in our DNA,” he said. “There’s real science being done on why our connection to nature is so important.”
In many ways, biophilic design is intuitive, Roberts said. He often hones in on what makes nature so attractive, like the variety of plant heights and colors found in a meadow or the shadows cast by trees on the forest floor. One recent apartment project he helped design has a pattern on the façade inspired by water ripples.
“There’s a lot going on in those natural places, and how do we recreate that in the places where we live and work?” Roberts said. “I’m looking at (design) through a biophilic lens.”
Variety found in nature is one reason why building façades often are more intriguing if they have varying window sizes or undulate and erode like a geologic form, he said. Biophilic design also responds to primal desires, such as providing vantage points where people can overlook a room or seating where they feel protected.
With people spending the majority of their time indoors, it’s important to remember our roots, Isle said.
“We’ve separated ourselves from nature,” she said. “Biophilia is a reminder that nature supports us in so many ways.”
To learn more about biophilic design, please contact
Nicole Isle, Chief Sustainability Strategist, at [email protected]
This article was originally published in the Portland Daily Journal of Commerce on September 10, 2014
“Fanatic Attention to Detail” is a cultural commitment at Glumac. Whether we’re working on drawings, specifications, qualification packages or planning our next client event, we strive for perfection in every way possible. To this end, we are committed to providing quality training for our employees. In June, Glumac hosted “Base Camp” for 21 of our recent graduates and new employees. Mechanical, electrical and plumbing engineers from each of our ten offices, including three from Shanghai, attended this week-long event in Sacramento, CA.
Base Camp was an intense and informative week of industry cross-training. Attendees were immersed in a variety of MEP topics, as expected. More importantly, they were enlightened by experts in Architecture, Contracting, Structural Design, Commissioning, Energy Analysis, and Manufacturing.
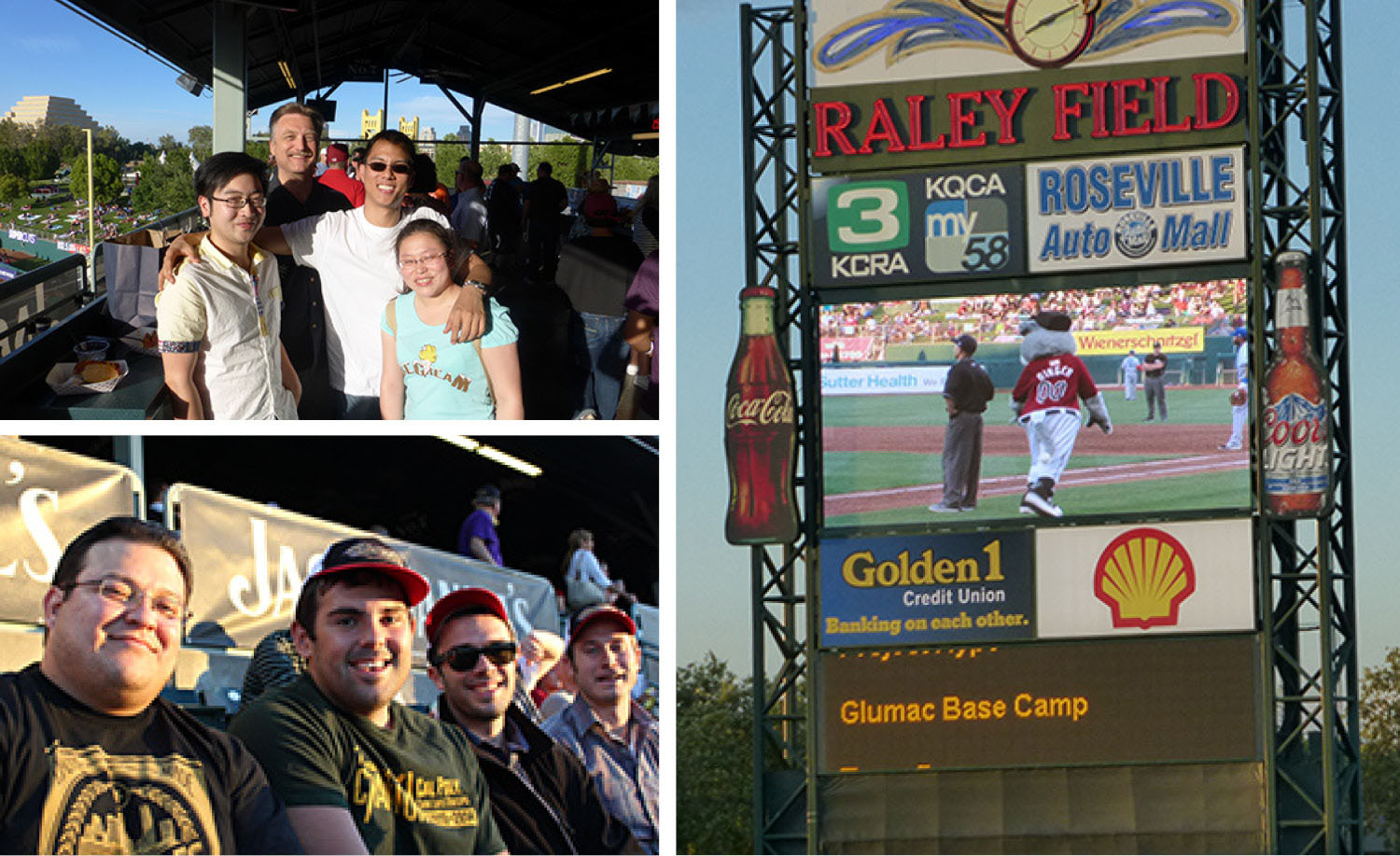
The training week also included a visit to an equipment manufacturing plant and even some fun team building trips to Lake Natoma and a Triple A baseball game. Recognizing these young engineers as the future of our industry, Glumac is investing in educating them about the issues that our clients face throughout the life of a project. As with any new young professional, there are opportunities to round out knowledge through focused, mentor-based training and give them the right tools to improve on service delivery in addition to on-job training. The goal is helping these young engineers reach their potential by providing the right support and attention.
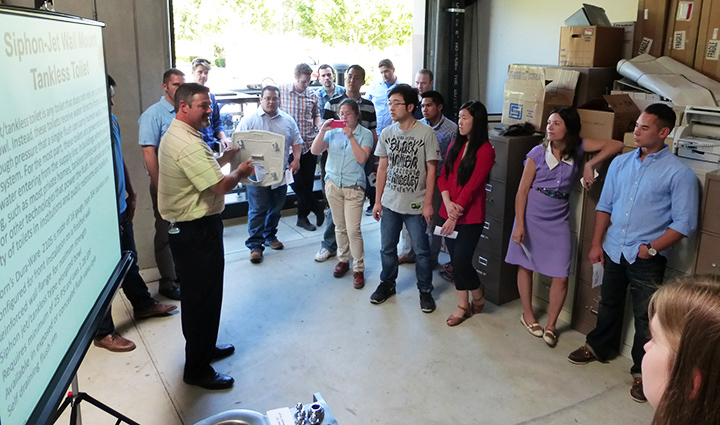
Charlie Smith, Plumbing/Mechanical Specification Consultant at Elmco Associates, who served as a guest speaker at Base Camp, said, “You have a great group of young engineers coming on board. It is obvious they will be a huge asset.”
Among our guest speakers was also Architect Jack Paddon, Principal of Williams + Paddon Architects + Planners, Inc., who shared his perspective.
“What a great experience for those who are just entering the work place to be immersed in standards of good professional practices that include not only the what’s and why’s, but also the philosophical why-not’s! These Base Campers will be our future industry leaders not so far in the future and I was pleased to have an opportunity share from the architect’s perspective.”
Training days were congenial and engaging. Young engineers asked questions and shared challenges they have encountered in designing specific facilities and in different market sectors. Experienced, senior professionals shared their wisdom and solutions from their past.
Joe Dillingham, MEP Coordinator, DPR Construction, shared a General Contractor’s point of view. “With an interactive dialogue, I presented questions to the group and they responded with intelligent answers, leading to more discussion. I was happy to share my experiences with them.”
We take pride in our industry’s future, and are enthusiastic about the refreshing outlook of our rising engineers. We believe “Fanatic Attention to Detail” is critical to success in engineering and we look forward to training world-class “engineers for a sustainable future.”
Our sincere gratitude to:
Jack Paddon – Williams + Paddon Architects + Planners, Inc
Joe Dillingham – DPR Construction
Roger Fuller – Sacramento County Chief Building Official (Retired)
Todd Noce – Mason Industries
Charlie Smith and Dave Moore – Elmco Associates
Ryan Culver – Associated Lighting Representatives, Inc (ALR)
Mel Melliza – Associated Lighting Representatives, Inc (ALR)
Rob Fuentes – Schneider Electric
Gregg Vlahakis and Joachim Gensel – Viking Sprinkler
Chris Stewart – Norman S Wright (HVAC Equipment)
Marc Sorge- Greenheck Fans Scott Athey – Industrial Electronic Systems
Located in the heart of the Financial District in downtown Los Angeles, Glumac’s new office space sets a precedent for ultra-efficient tenant improvement projects. The office relocation is an opportunity for the firm to chart innovative strategies for existing high-rise buildings by pursuing Petal Certification under the Living Building Challenge (LBC).
The LBC is often considered the most rigorous green building performance standard. It calls for the creation of building projects at all scales that operate as cleanly, beautifully and efficiently as nature’s architecture. To achieve certification under the LBC, projects must meet a series of ambitious performance requirements over a minimum of 12 months of continuous occupancy. Glumac has taken this unique approach to its new LA office location and will establish a learning laboratory3580 where the performance of these sustainable strategies can be monitored and observed firsthand.
A program of the International Living Future Institute (ILFI), the LBC is organized into seven environmental and social impact areas, called Petals. From these Petals stem 20 Design Imperatives. While fulfilling all LBC imperatives is the ultimate goal, achieving multiple requirements through Petal Certification is also a significant achievement. Four of the seven environmental and social impact categories must be completed for a project to be awarded Petal Certification, one of which must be either the Net-Zero Energy, the Net-Zero Water, or the Materials Petal.
With a focus on Net-Zero Energy, as well as the Site, Equity and Beauty Petals, the Glumac LA project is in the running to become the 2nd Living Building Challenge Petal Certified tenant improvement project in the world and the first of its kind in Los Angeles. In collaboration with ILFI, Gensler, Shimizu and GIGA, Glumac has also just opened its new Shanghai office, the first Living Building Certification-targeted project in Asia. In these twin efforts, the design teams have applied insight stemmed from Glumac’s high-performing LEED Platinum offices in Irvine, Portland, and Silicon Valley.
Petal to the Mettle
Occupying the 23rd floor of the Aon Center, the new Los Angeles office design is centered on the idea of collaboration and connectivity. The 17,500 sqft open office plan design, developed by Gensler, allows for natural daylighting and encourages a collective work ethos.
Open workspaces are organized in eight-person “neighborhoods” that boost team-building opportunities for specific projects or market types. Each workstation is identical, facilitating flexibility to move individuals or groups, as project needs change. Smaller closed breakout spaces and meeting areas are adjacent to open workspaces for focused discussions.
Collaboration spaces can also be found in break out rooms, innovation labs, and a large open kitchen that lie just beyond the lobby. The kitchen, aptly referred to as Downtown, acts as a communal activity hub with a long table of Forest Stewardship Council wood at its center, allowing staff and clients to meet and freely exchange ideas.
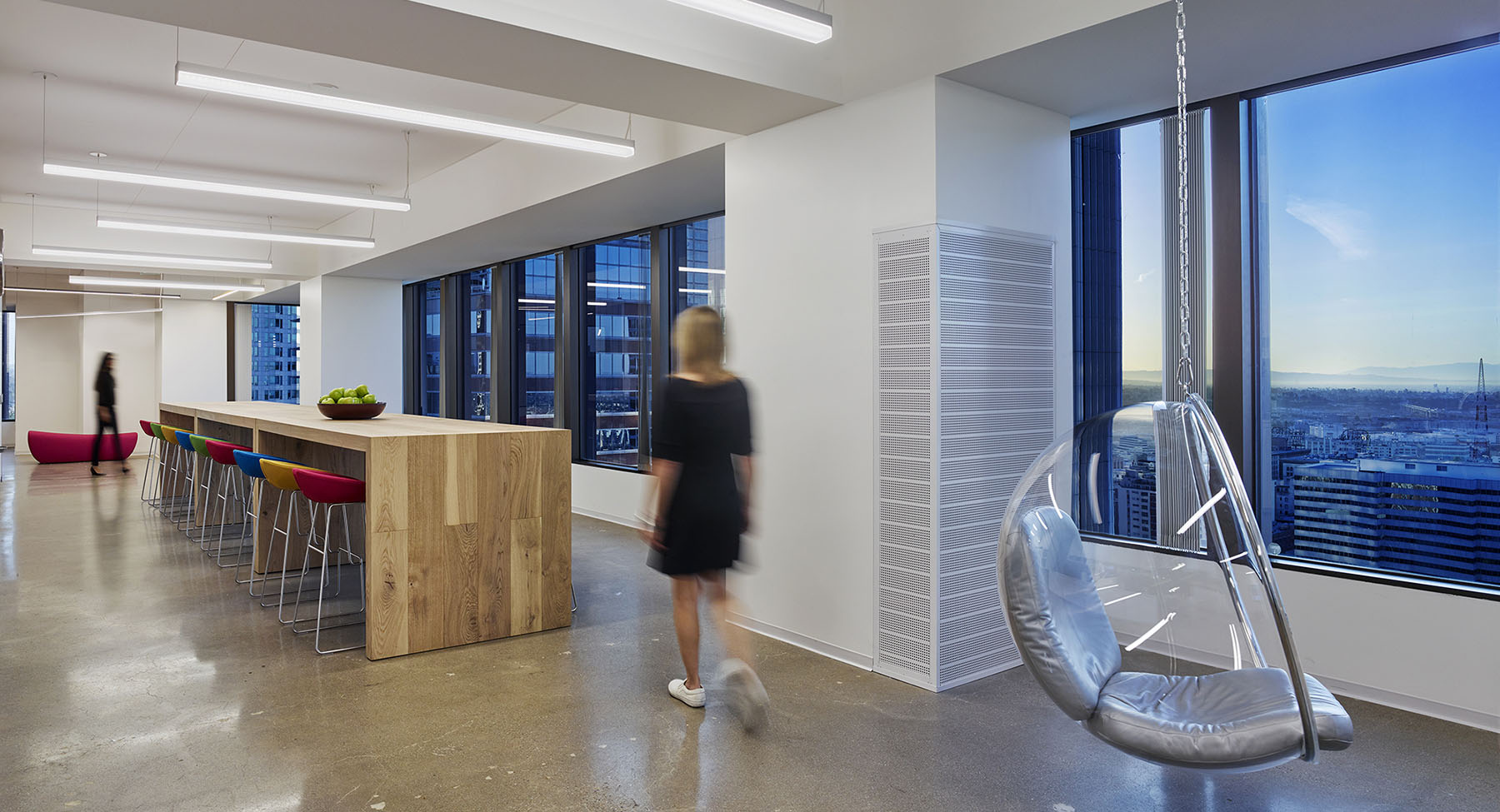
Managing Principal Jacob Chan explains, “The kitchen has always been the center of gravity where people mingle, talk, act together and brainstorm. We wanted it to be the cornerstone of the interactive space.” This design allows for an adaptable, expansive work environment that creates opportunities for a new level of mobility and connectivity for Glumac.
Site + Equity
Completed in 1973, the Aon Center is a 62-story, modernist skyscraper designed by Charles Luckman and constructed by CL Peck Contractor. The large window openings allow employees to take in 360° views of Los Angeles and the surrounding San Gabriel Mountains from the 23rd floor. Site proximity to Metro buses, trains, and bike lanes allows convenient commuting options beyond the single-occupancy vehicle. The dense urban location of the project provides ample opportunity for Glumac staff to engage LA’s vibrant downtown community and culture, enjoying parks, restaurants, cultural centers, and major clients in nearby buildings.
To honor the “Habitat Exchange” imperative, Glumac will collaborate with a local Land Trust that preserves and creates urban parks and gardens. As stewards of sustainability, Glumac’s concern is protecting natural habitat within the urban landscape by fostering a reciprocal relationship with the community.
An additional benefit to choosing an existing “predeveloped” site like the Aon Center is that the project satisfies LBC’s Equity Petal “Rights to Nature” Imperative by not emitting air pollution. The building does not use fossil fuels. With no combustion on site, the building does not inhibit adjacent properties from enjoying fresh air and the ability to naturally ventilate their spaces.
Net-Zero Innovations for High-Rise Buildings
The primary intention for the Aon Center retrofit project is to achieve net-zero energy for the new Glumac office. One of the most challenging aspects the team faced was the lack of direct access to renewable energy sources. Typical with most existing towers, modification of the roof and the building façade were not permitted, which limited the opportunity to generate renewable power onsite. The Glumac team assessed the building for alternative methods to offset energy consumption of the 23rd floor, with the goal of pushing energy back to the grid.
Glumac first considered the energy consumption of the entire building and recognized the constant heat load produced by the air-cooled chillers that serve a large data center located on the 4th floor. With typical air-cooled chillers, heat from the space that is being cooled gets rejected to the atmosphere. In order to close the loop, Glumac designed a base building retrofit with the intent of producing chilled water to condition the data center, using heat recovery chillers (HRC) and repurposing the waste heat from that process to serve a new hot water loop for space heating. The hot water loop will replace the existing electric resistance heating coils in the main air-handlers that currently provide the heating for the building. The new HRC will also be used in lieu of the existing centrifugal chillers during low-load conditions. Additionally, since the existing chilled water supply of the building is nearing its maximum capacity, the HRC will be used to serve future process cooling loads.
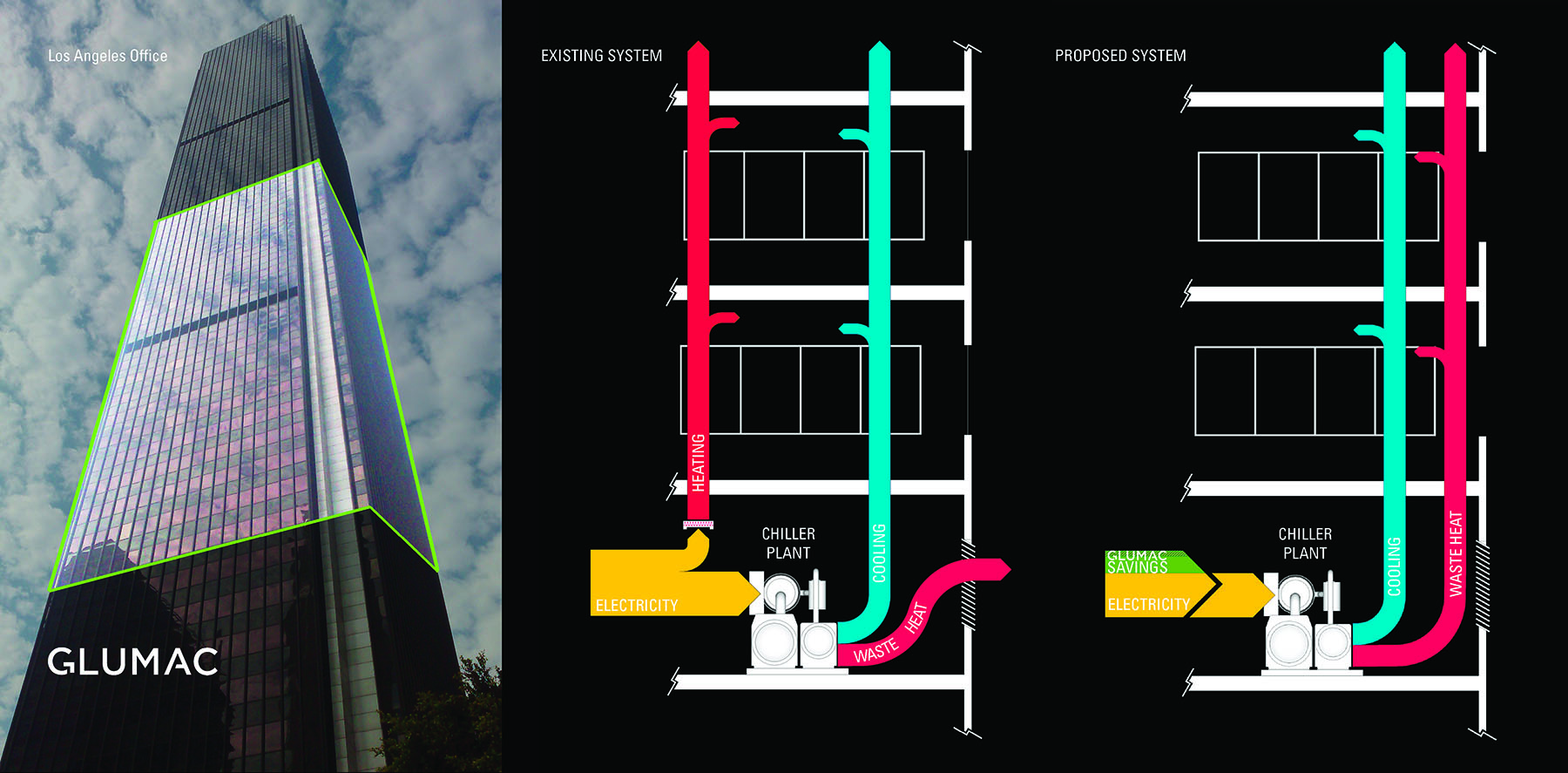
The free heat will now be supplied to 20 floors of the tower, which is significantly more energy than the Glumac tenant space will consume over the course of a year. Therefore, the space will be net-zero energy.
Through an iterative discovery process, we integrated a net-zero energy strategy based on a whole building heat recovery retrofit of the central chiller system. The project team initiated a dialogue with the building owner early in the process. Once the design approach and potential for savings were demonstrated, the owner quickly approved the implementation of the system. As a result, Glumac’s pioneering approach to heat recovery paves the way for tenants to go after LBC in high-rise buildings. This strategy has now been formalized in the LBC Dialogue for other projects to pursue.
Overall Energy Savings
It is anticipated that LADWP may provide incentives of $0.08/kWh saved through the Custom Performance Program (CPP), which would be approximately $60,202. Therefore, the net investment cost of the project would be $380,098. The total energy savings realized by replacing the electric resistance coils with hot water coils and using the HRC for after-hours operation is approximately $752,530 ($109,869) annually. The simple payback for this scenario is 4 years, or 3.5 including the CPP incentive.
HVAC Systems
Net-zero energy operation requires work to reduce energy demand as well as maximizing production. In order to reduce overall energy use in the office space, the Glumac team included high-efficiency HVAC systems and state-of-the-art HVAC and lighting controls.
Cooling for the open office area comes from chilled sails, radiant panels, and VAV terminal units. The chilled sails and radiant panels are highly energy efficient since providing cooling via water is far more energy efficient than using air. The VAV terminal units provide fresh air and cooling to the open office as well as the rest of the floor. Cooling for the reception area is provided using displacement ventilation, which is more efficient than typical overhead mixing systems because air can be supplied at higher temperatures. This means that the supply air doesn’t need to be cooled down as much, which results in energy savings. Heating for the open office area is provided via hydronic radiator heaters at the perimeter, and heating for the remainder of the office is via reheat coils at VAV terminal units. Hydronic heating is much more energy efficient than the electric heating that the 23rd floor previously utilized.
Energy usage will also be reduced with the innovative HVAC controls. The HVAC control system will allow occupants to electronically vote on whether they are too hot, comfortable, or too cold. If enough people for a given zone vote the same way, the HVAC system will react and make adjustments as necessary to make the zone more comfortable. The HVAC control system will also learn occupant preferences and further reduce energy use by adjusting temperature set points and widening dead bands.
Plumbing
The core toilets have been renovated with the latest technology in water-saving fixtures and faucets. But, the innovation goes beyond the core walls. The drinking fountains were replaced with touch-free water bottle refill units. A separate water filtration system is also installed in the kitchen.
Lighting Systems
With the work of the Glumac’s IES award-winning Lighting Studio, the space lighting design is the first of its kind and highly energy efficient. Our lighting designers work on the premise of “putting the light where it is needed.” Rather than installing high wattage fixtures 9’ in the air to illuminate a 30” high desk, the fixtures are mounted only 18” above the desk surface. Programmable and dimmable Light Emitting Diode (LED) lamps are also used to the greatest extent possible, which is likely the course of the future. This greatly reduces energy consumption as well as providing the user with ready control of the fixture.
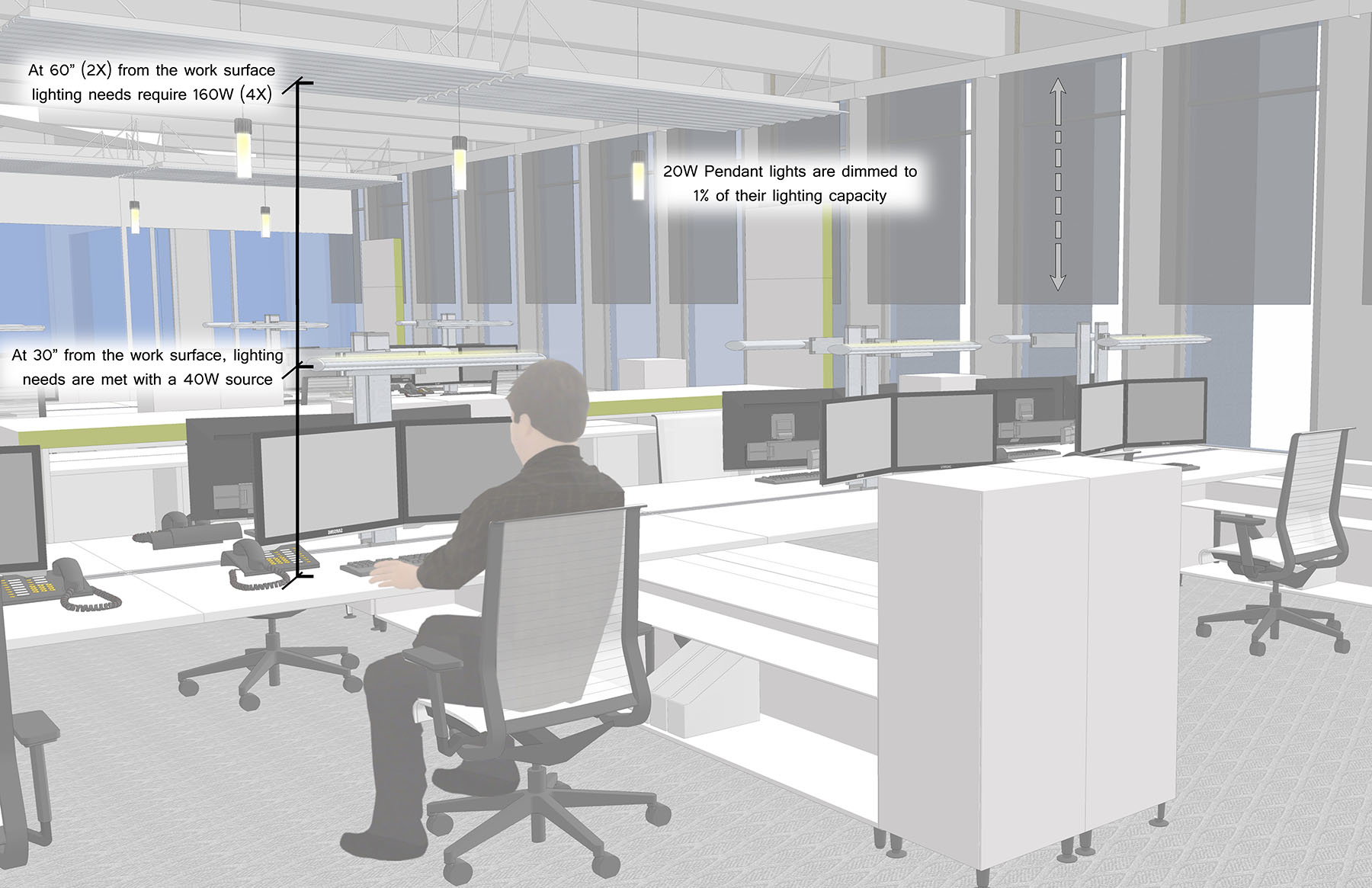
Lighting Controls
Glumac has installed innovative and user-friendly controls to create energy-efficient lighting schemes in each of the spaces. In general, spaces are provided with “vacancy sensors” instead of only occupancy sensors. This leaves people to decide when to turn on lighting, not a machine. Only spaces with no access to daylight are provided with “occupancy sensors.” Lighting controls for each “neighborhood” are configured as follows:
- A wall switch at the entrance to each neighborhood allows you to turn on the task/ ambient lighting at an individual’s desks, with one switch controlling the two fixtures closest to the windows, and the second turning on the two fixtures closest to the corridor.
- A vacancy sensor in the ceiling will turn off fixtures as the space is vacated during the day.
- A photo sensor will modulate the electric lighting levels automatically as daylight is available.
- A wall switch at the end of the collaboration table will turn on the pendants hanging overhead.
- An LED art light, controlled by an occupancy sensor, is mounted to highlight the display wall on the corridor side of the collaboration table.
- Lighting controls within day lit, enclosed spaces are, again, automated through “vacancy” sensors. The lighting will not come on unless occupants feel the illumination levels are inadequate and activate the switch for electric lighting. The lights will turn off automatically once occupants leave.
”Beautiful in Los Angeles”
Glumac’s new office was thoughtfully designed with an emphasis on lightness and a clean color palette. Elements of the project include linear fluorescent fixtures throughout the space, and playful mod hanging chairs in the lobby. The site lines within the space are unobstructed allowing for dramatic views of the city. All furniture and fixtures were selected for ease of use and a minimal design aesthetic.
In the lobby of the new office, Glumac is planning a central dashboard that aggregates energy and water data in a graphical display to educate occupants about their sustainability efforts. Developed in collaboration with Delta Controls, the dashboard uses coaching feedback mechanisms to quantify performance and teach/empower users how to improve their energy performance. A simple avatar relays information back to the user such as energy consumption, energy generation for the heat recovery and consumption, and when light power density too high and how it can be adjusted.
In the near future once commissioning is complete, the office will be outfitted with Comfy, a comfort control system designed by Building Robotics. Comfy will allow employees to vote via a web-based interface to indicate whether they are too hot, “Comfy”, or too cold. If enough people for a given zone vote the same way, the HVAC system will adjust and react as necessary to achieve thermal comfort. The control system will learn our preferences and optimize the HVAC system to reduce energy use. We intend to post information from both the dashboard and Comfy will be accessible online through Glumac’s website to track the energy performance of the Los Angeles office.
Sharing New Heights of Sustainability
A major component of the Living Building Challenge is using projects as educational tools to drive further change in the AEC industry. Glumac hosts tours of the new office in order to exemplify the unique HVAC systems implemented and other features related to the Living Building Challenge. In an effort to make the space a learning laboratory and prove that our office is truly net zero, we have installed meters to collect and trend data for our heating, cooling, and electrical systems. The meters allow us to not only track our energy usage, but they also enable us to proactively reduce our energy usage. The results will be displayed on the energy dashboard to demonstrate how we are doing each month and to provide feedback on how we can further reduce our energy usage.
We invite you to get in touch, come and see the new space, and see how we bring advanced green building strategies to existing buildings.
Trends come and go in every industry. Some end up being passing fads and others transform their respective industries. It is likely history will show that some of the current data center modularity trends added little value to the industry, while others helped sustainably transform it.
Modularity is one such data center trend that could forever change the future of the industry. There are a myriad of “modular” data center variations. Some of the options include:
- Containers: Referring to containerized data centers that are an all-inclusive “data center in a box.” Shipping container-sized modules that are fully functional data centers with single points of connection for power, IT, water, and sewer.
- Pre-planned stick built: Modularity refers to MEP/IT capacity building blocks that allow the next “chunk” of capacity to be added in definable and repeatable “bite sized-chunks.” The construction around this definition still refers to stick-built construction.
- Pre-Fabricated: Modularity refers to MEP components that are definable bite-sized chunks but are also in part pre-fabricated off site and brought in as fully functional and tested, ready-to-go MEP/IT components.
Glumac has designed over 4M sf of data center whitespace. In our opinion, all mission critical projects have critical project constraints (cost, efficiency, speed to market, quality, etc.) that might benefit from a modular approach. Traditionally, two of the biggest challenges with data center builds are capital outlay and speed to market. The traditional brick and mortar data center is generally expensive with long lead times. Modular builds can not only help a client save money and time, but also allow them to better match their inherent growth, enabling a more sustainable business model with less stranded capacity.
What are some of the advantages of a modular approach compared to a traditional build?
1) Improved Speed of Deployment:

- Traditional construction methods are dependent on the determined project critical path. Certain aspects of a project build cannot start until others have been completed. In the data center industry, electrical buy-out and electrical construction is always on the project critical path. In theory, taking any item off the project critical path allows potential time to be saved (Figure 1).
- There are pre-assembled modular solutions that allow quicker time frames from order to deployment. As a standardized solution, modules can be ordered, manufactured, customized and delivered to the data center site in relatively short time frames. Any assembly work done off-site also means that the site construction can progress in parallel, instead of in series toward completion.
2) Potentially Higher Quality:
- Pre-manufactured components are typically manufactured in a controlled environment. Theoretically, this enables better working conditions, better QA/QC, pre-service testing and even commissioning of the component before shipping to the site. There are risks and costs involved in shipping. These need to be weighed as part of the decision making process.
3) Cost Efficiency:
A modular data center build can also reduce upfront capital outlay and stranded capacity. The modular approach can provide an “as needed” deployment of IT, electrical and mechanical capacities to accurately match the clients current IT demands and allow for quick deployment when future capacity is required. Therefore, a modular build allows potentially smaller initial builds with a predefined roadmap building block strategy for subsequent additional MEP/IT capacity. Basically, build what you need when you need it (Image 3).
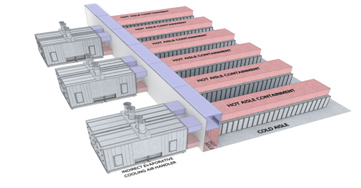
- With a repeatable, standardized design, it is easy to match demand and scale infrastructure quickly. The only limitations on scale for a modular data center are the supporting infrastructure at the data center site and the available land. Another characteristic of modular scalability is that modules can be easily replaced when obsolete, or if a technology refresh is in order.
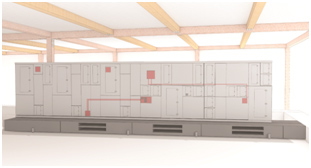
- Potential Labor Savings: A manufacturing facility in Nevada may employ workers with an average wage multiplier of 1. If the data center was built in New York City, the cost of labor might have a multiplier of 1.4 or higher. Having components pre-manufactured in Nevada, would save the project 40% on the labor associated with the pre-manufactured equipment.
4) Controlled Technology Relevance
- Technology in data centers is ever evolving and changing at rapid rates. The modular approach to building “just-in-time capacity delivery” allows data center IT personnel to implement current technologies, while still allowing future technological advances to be utilized when future MEP/IT capacity is required.
In summary, Glumac’s Data Center group feels that sustainable modularity will help transform the data center industry and get users to think in terms of “build as required MEP/IT capacity.” Capacity additions/refreshes can have different looks, but data centers are just too expensive, IT needs are too dynamic and IT technology is too fluid to not consider the modularity approach to data center capacity decisions.
For further information on design approaches in the data center market, please contact Sam Graves at [email protected].